Transportador de banda metálica Superbelt®
Ideal para el transporte eficiente y seguro de grandes cantidades de chatarra de aluminio
La recuperación y tratamiento de la chatarra es un tema de creciente importancia en las fundiciones de aluminio.
La calidad de la chatarra, el ahorro de mano de obra, el consumo de energía, la seguridad de los trabajadores, son todos factores que se ven afectados, para bien o para mal, por la elección del sistema de transporte de chatarra.
Gracias a su diseño único, el transportador Superbelt® ofrece a las fundiciones de aluminio ventajas y una flexibilidad mayor que las carretillas elevadoras, las bandas de goma y los transportadores de cadena, en el manejo de los desechos de producción (p. ej., mazarotas, bebederos, canaletas). Es generalmente utilizado para alimentar prensas, trituradoras y hornos de refundición, o para transportar chatarra desde el proceso de fundición a presión hasta el depósito de chatarra.
Fiabilidad elevada
El transportador Superbelt® consta de placas de acero parcialmente sobrepuestas, conectadas a una malla metálica doble.
El diseño de la cinta se basa en un concepto multi-enlace que garantiza elevada fiabilidad, mantenimiento mínimo y un funcionamiento regular, sin problemas. Incluso en el caso de daños a la malla, el transportador seguirá funcionando, sin paradas repentinas, hasta la próxima parada para el mantenimiento programado.
El funcionamiento sin problemas ayuda a preservar la productividad y la rentabilidad de toda la planta y se traduce en una mayor eficiencia y un tiempo de operación más largo, para un funcionamiento 24 horas al día, 7 días a la semana.
Eliminación de atascos
Debido a bordes afilados, protuberancias y formas irregulares, la chatarra de aluminio se atasca en las placas de la cinta.
El transportador Superbelt® soluciona este problema gracias a la perfecta sobreposición de las placas que crea un canal de transporte prácticamente sellado y evita que el material transportado se atasque.
Mayor seguridad para los operadores
Al automatizar completamente el proceso de manejo de la chatarra, el transportador Superbelt® minimiza los riesgos para la seguridad de los operadores relacionados con el manejo de la chatarra y el tránsito de carretillas elevadoras dentro de la planta.
Además, las altas protecciones laterales que siguen el perfil del transportador en toda su longitud evitan que el material se escape durante el transporte, protegiendo así a los operadores del daño causado por el material fugitivo.
Bajo consumo de energía
Diseñado para evitar la fricción por deslizamiento entre las piezas móviles, el transportador Superbelt® es extremadamente eficiente desde el punto de vista energético. De hecho, el consumo de energía es alrededor de una décima parte del consumo esperado por los transportadores vibrantes tradicionales.
Pesaje del material (opcional)
Cuando sea necesario, el transportador Superbelt® también permite el pesaje continuo del material transportado. En este caso, la sección de la cinta está equipada con un marco especial con células de carga y una unidad de control electrónico para el cálculo en tiempo real de la masa y la capacidad.
La capacidad real se determina combinando la velocidad de la cinta, detectada por un codificador, y la señal de pesaje suministrada por las células de carga.
Algunas historias de éxito
Italia
Trasporto dei rottami in alluminio
Fonderia di alluminio
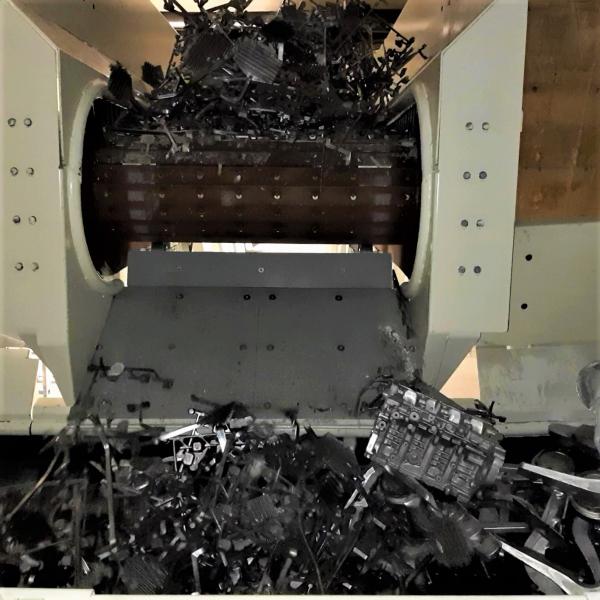
I trasportatori Superbelt® hanno offerto maggiore efficienza, ridotto il tempo di ciclo della movimentazione del materiale e aumentato la sicurezza per gli operatori.
Il Cliente
La fonderia è specializzata in fusioni in alluminio per l'industria automobilistica, utilizzando le tecnologie Lost Foam, Low Pressure e High Pressure Die Casting (HPDC).
La Sfida
Prima dell'installazione del trasportatore Superbelt®, le fusioni scartate provenienti dalle macchine HPDC situate al piano superiore venivano scaricate manualmente in contenitori situati nel seminterrato. Poiché queste operazioni comportavano gravi preoccupazioni per la sicurezza, il Cliente ha deciso di automatizzare il processo di gestione dei rottami.
La Soluzione
Installato nel seminterrato, un lungo trasportatore Superbelt® raccoglie le materozze, le sponde e le fusioni scartate provenienti da 7 macchine HPDC situate al piano superiore. Questo trasportatore trasferisce il materiale a un trasportatore Superbelt® più corto che sale all'esterno del seminterrato per scaricare il materiale nei contenitori per rottami destinati al successivo rifusione.