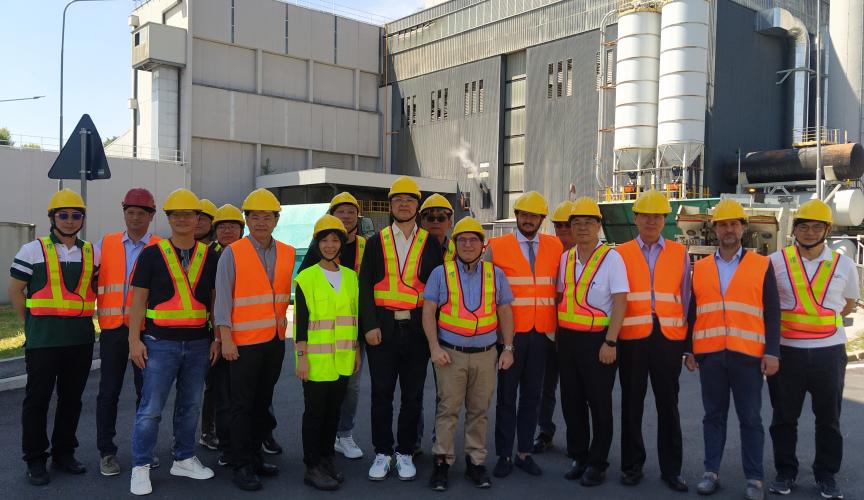
On July 2nd, the Brianza Energia Ambiente WtE plant in Desio, Italy hosted a delegation from Kaohsiung, Taiwan's second-largest city with over 2.7 million residents. Led by the deputy mayor, the delegation included representatives from the city's Environmental Protection Office, Public Works Office, and Taiwanese environmental services companies.
The visit aimed to learn about the plant's incinerator bottom ash (IBA) extraction process, which utilizes Magaldi's innovative dry extraction system.
In 2016, Magaldi worked on a complete overhaul of the IBA extraction system at the Desio plant. They replaced the outdated wet system, in operation since the plant opened in 1976, with the innovative Magaldi Ecobelt® WA (waste ash) dry extraction system.
«The dry extraction method avoids wastewater and significantly reduces the environmental impact of the process, with complete resource recovery», explained the plant's technical director, Giorgio Tominetti. «The metallic fraction is sent to smelter, and the inert fraction is sent to cement factories. This process enables to recover not just iron and aluminum, but also precious metals».
Thanks to this system, the Desio WtE plant can divert 15,000 tons of IBA per year to material recovery.
The Taiwanese delegation, which is seeking to reduce landfill disposal on the island, was impressed by the minimal environmental impact of the Magaldi technology. Onyx Ta-Ho, the Taiwanese subsidiary of the French giant Veolia that operates hundreds of WtE plants worldwide, has already adopted the Ecobelt® WA system for its Renwu and Lutsao WtE plants and was able to see the advantages of this technology firsthand during their visit to Desio.
«The dry IBA extraction system represents a significant contribution to achieving an effective circular economy model», stated Paolo Magaldi, CEO of the Magaldi Group. «The ability to reuse the inert fraction in other production processes and recycle recovered metals, reintroducing them into the economy in a sustainable cycle, increases the overall functionality of the process and reduces natural resource consumption».
«We're grateful to the Kaohsiung delegation for visiting our plant», declared Mario Carlo Novara, the president of Brianza Energia Ambiente. «Their interest confirms the quality of the environmentally friendly service that BEA has always provided to our local community. This year, we celebrate 60 years of this innovation-driven mission, which still has much more to offer».