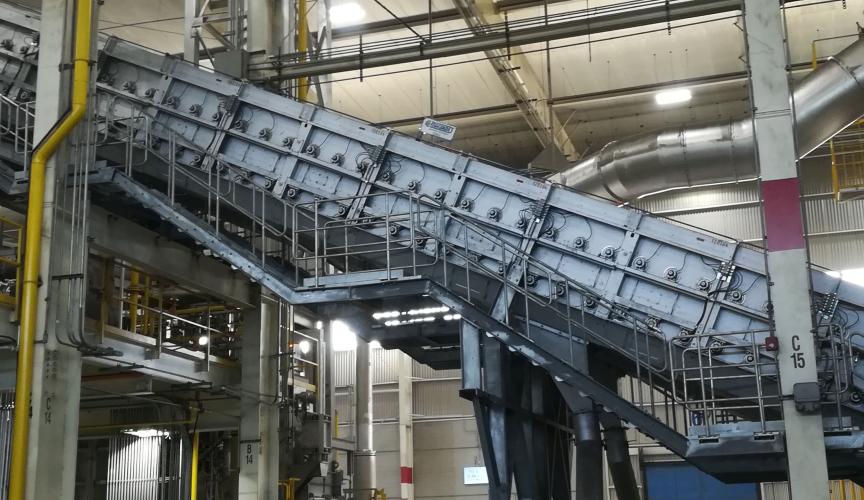
Magaldi Ecobelt® technology to improve aluminum recycling by allowing to re-use thermal energy from upstream processes
Magaldi repeated the successful experience achieved at Novelis’ Nachterstedt Recycling Center, by supplying its Ecobelt® technology to handle hot aluminum shreds to Logan recycling plant in Kentucky.
With a continuous production of 20 t/h for each line, the Ecobelt® systems connect in a reliable way two delacquering kilns with the downstream furnaces.
SECONDARY ALUMINUM SMELTING
Secondary Aluminum Smelting is the process of recycling aluminum scrap into aluminum that can be used and recycled over and over again in a true closed-loop process.
The increased adoption of recycled aluminum has created significant economic and environmental benefits for both industry and consumers. Currently, more than 90% of aluminum used in automotive and construction applications is recycled and the trend is constantly growing in other industrial sectors because of the economic and environmental benefits it provides. In fact, secondary aluminum production not only needs less energy (recycling scrap aluminum requires only 5% of the energy used to make new aluminum), it also reduces landfill waste and greenhouse gas emissions.
Once collected and sorted, aluminum scrap is decoated- typically through the use of a rotary kiln – to remove coatings and contaminants. From rotary de-coaters, hot shreds (at about 500 °C) are then conveyed to the recycling furnace and turned into molten aluminum to be casted into ingots or billets, ready for subsequent processing into new aluminum products.
THE ECOBELT® TECHNOLOGY TO HANDLE HOT RECYCLED ALUMINUM
Magaldi has developed a system able to reliably handle hot shreds (at about 500°C), connecting the rotary de-coater with the downstream melting furnace. The Ecobelt® is a steel belt conveyor, completely enclosed in a steel casing, able to handle hot materials with aggressive chemicals, and heavy or sharp products, ensuring a safe and environmentally friendly operation. Its ability to guarantee high reliability makes it the appropriate solution for secondary smelters and aluminum recycling facilities.
Usually employed to convey hot shreds, conventional apron-based conveyors enclosed in casings are not able to avoid heat dispersion. Moreover, directly exposed to high temperatures and dusty material, bushings and chain links need frequent greasing to avoid excessive wear thus requiring frequent shutdowns to open the casing and lubricate. In addition, chain links and guide rails often break due to dust accumulation on the bottom of the conveyor. Unlike apron-conveyors, the Ecobelt® prevents dust dispersion into the environment and ensures the lowest temperature drop thus allowing to re-use thermal energy released from upstream processes. In fact, its core technology is the Superbelt®, a steel belt conveyor made of partially overlapping steel pans bolted on a steel double-wire mesh, that form a virtually sealed belt conveyor. Although enclosed in a steel casing, maintenance activities are very easy: all bearings are installed outside to allow trouble-free maintenance at any time and lubrication with the belt in operation. Furthermore, the absence of chains, pinions and sprockets guarantees a low wear and tear and a longer service life.

THE EXPERIENCE AT LOGAN ALUMINUM
RECYCLING CENTER
The successful experience achieved by Magaldi at Novelis Sheet Ingot GmbH paved the way for a new challenging experience in the aluminum recycling industry. In September 2016, Logan Aluminum Inc. – leading manufacturer of flat rolled aluminum sheet for the beverage can market in U.S. - awarded Magaldi with a contract for the turn-key installation of a complete Hot Shred Conveyance System for its new Recycling Center located in Russelville, Kentucky. Logan was looking for a dependable technology able to improve all aspects related to safety, process capability and spare parts requirements. The attempt to use a chain conveyor had not been successful due to the inability to perform according to the plant requirements. After simulating the plant operational conditions so to better customize the offer, Magaldi signed a contract to supply two Ecobelts® to convey 40 t/h of hot aluminum shreds from the delacquering kilns to the downstream melting furnaces. The first Ecobelt® became operational on Summer 2017 while the second conveyor on October 2018. In the same year, two further Ecobelt® systems were commissioned to handle up to 18 t/h each of aluminum at 560°C.
Ecobelt® Length: 44.000 mm
Width: 800 mm
Height: 5.000 mm
Capacity: 16 t/h
Temperature: 580°C
Handled Material: Aluminum shreds
Ecobelt® Length: 7.045 mm
Width: 800 mm
Height: 3.405 mm
Capacity: 18 t/h
Temperature: 560 °C
Handled Material: Aluminum shreds
Ecobelt® Length: 7.045 mm
Width: 800 mm
Height: 3.405 mm
Capacity: 18 t/h
Temperature: 560 °C
Handled Material: Aluminum shreds