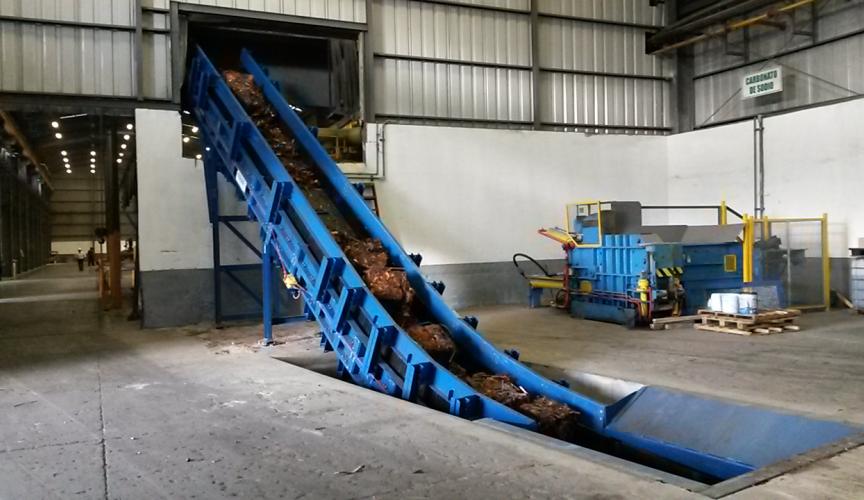
In 2017, a Mexican client was looking for a reliable and safer conveyor to replace the existing furnace charging system in its secondary copper smelting plant.
Stored in a bunker, the copper scraps were packed in bales by compressing press and unloaded into the vibrating feeder by a forklift tilting skip. The vibrating feeder moved on tracks in order to approach and unload the copper scraps into the furnace.
However, the forklift worked in a dangerous way since the vibrating platform was too high to be easily reached. Moreover, the overall material handling inside the plant was difficult and expensive.
In order to create a safer work environment and reduce the costs for material handling, the Client chose to install a Magaldi Superbelt® conveyor able to improve all aspects related to safety, reliability and process capability.
The Superbelt® has been equipped with a tailored loading hopper, installed in a pit under the floor, to allow operators to load copper scraps easily and manage the system in batch.
Despite the conveyor‘ steep inclination (35°), copper bales are handled smoothly thanks to the proper edge of the belt plates and some cleats which help the material not to roll backwards on the belt.