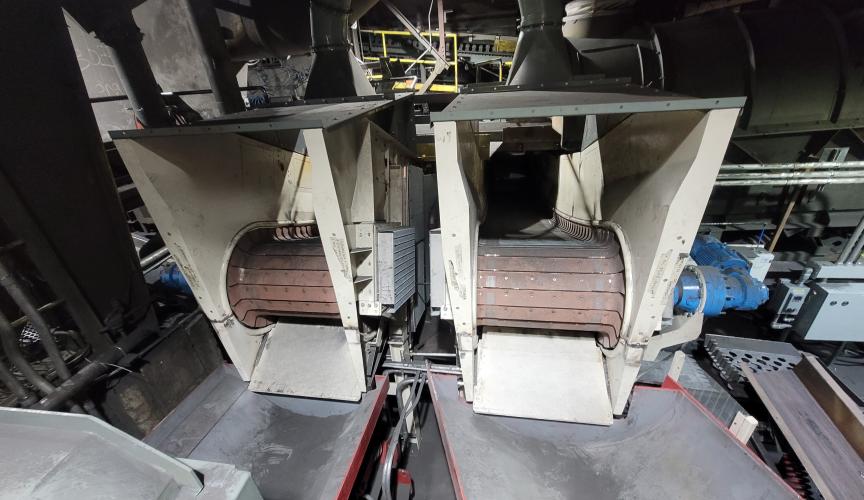
Waupaca Foundry’s Marinette, WI, plant was the site of a re-engineering project late last year, replacing a 30-year-old vibratory system with two conveyors to conduct gating and sprue materials from the mold shakeout line. The 16-day project had been in development since 2022 and required an extensive rebuilding of that area of the plant.
“Preparation and planning were critical leading into the project due to the scope of work required given the defined shutdown install window,” said Jarrod Osborn, vice president of manufacturing engineering for Waupaca Foundry.
In place of the vibratory system, there are now two, parallel Magaldi conveyor systems, and the change is expected to improve the foundry’s need for maintenance downtime by more than 50%.
The previous system was susceptible to jamming with the gating material separated from Waupaca’s ductile iron castings during shakeout. When the system stopped, six casting sorting lines had to pause too.
The Magaldi Superbelt conveyors can transport large volumes of gating and sprue material, improving transit uptime, and reducing energy and maintenance costs, which improves delivery times for finished castings to Waupaca Foundry customers.
“Because our system does not vibrate, the iron returns do not collect and jam up, silica dust is not generated, and the system is very quiet,” said Brandon Kruse, general manager of Magaldi Technologies LLC. “To minimize energy consumption, we can speed up or slow down the conveyor if we notice heavy tonnages because there’s an advanced algorithm in the system that tracks scrap loading on all six lines.”
The new conveyors also improve noise levels and indoor air quality in the workplace.
“The safety benefits of the new system were as important as the bottom-line savings,” according to Osborn. “By replacing the vibrating system, we significantly reduced the amount of airborne dust and created a healthier working environment for our team.”
Source: FOUNDRY Management & Technology