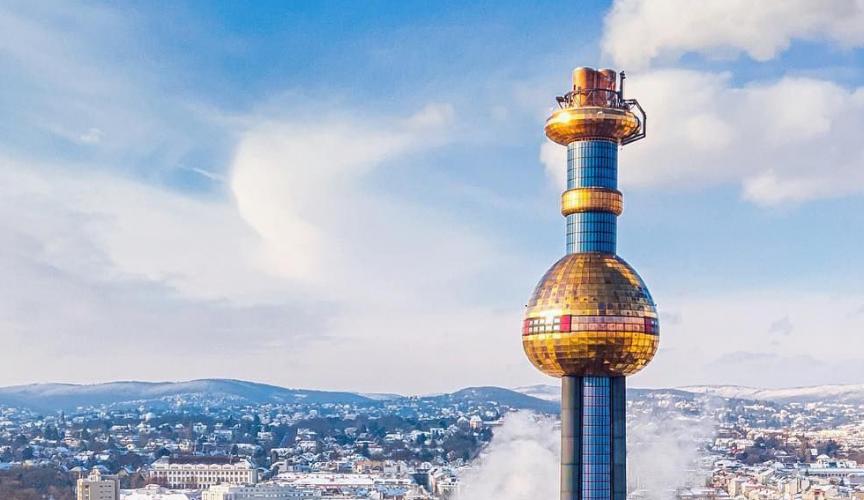
Last October 2017, Acea Ambiente opened the doors of its Waste-to-Energy plant in San Vittore del Lazio (Italy) to host the Magaldi Open Day dedicated to WtE. Since 2016 the plant is equipped with the Magaldi system for dry extraction, cooling and conveying of bottom ash.
WASTE-TO-ENERGY: STATE-OF-ART TECHNOLOGIES TO MOVE BEYOND ITS “DIRTY” REPUTATION
Economic growth is extremely energy dependent. The continuous increase in the global energy demand has created pressure on the supply of new energy resources. In fact, traditional sources are no longer able to withstand the energy requirement for the industrialized world. The steep increment in the utilization of fossil fuel in the past has resulted in an increase in pollution levels across the globe so that environmental protection is no longer an optional. The search for a safe and renewable energy supply has become one of the main governments’ alarms. A further problem governments are facing is the growing waste generation.
Municipal solid waste (MSW) generation is highly linked with factors like economic growth and industrial development. While industrialized Countries generate a higher amount of MSW due to the better economic standard, in developing Countries, urban expansion, population growth and technological development are contribute to increase MSW generation. Converting waste residues into electricity, heat or steam, the Waste-to-Energy (WtE) process can be considered as a potential alternative source of energy, economically viable and environmentally sustainable. Developed Countries have already realized the potential of WtE technologies for an effective municipal solid waste management. The development of advanced technologies for a cleaner and safer energy recovery process from waste has allowed to move beyond the “dirty” reputation of incinerators, allaying public fears to the point that ever more authorities are building WtE plants inside the urban setting (pic. 1). Europe is said to be the largest market for WtE technologies (47.6%), having embraced Waste-to- Energy as a way to reduce landfill growth as well as dependence on imported fuels. More and more Countries are ready to walk the same path.
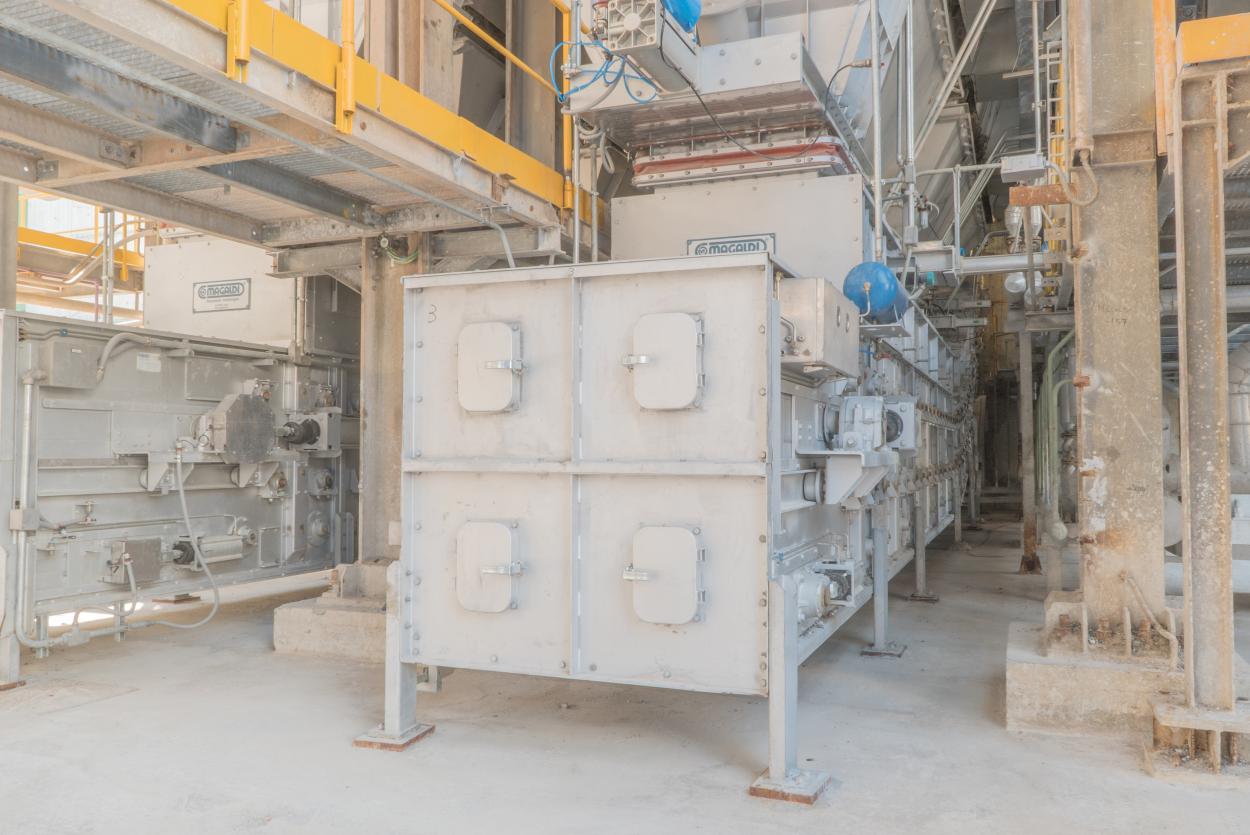
THE ECOBELT® WA TECHNOLOGY TO SUPPORT ENVIRONMENTAL PROTECTION AND IMPROVE THE ENERGY RECOVERY PROCESS IN WTE PLANTS
Waste-to-Energy is one of the most effective alternative energy options to reduce CO2 emissions and replace fossil fuels. It consists in generating energy in the form of electricity and/or heat from the primary treatment of waste. Burning in grate fired boilers at temperatures between 750°C and 1100°C, organic elements in MSW are destructed and converted into energy. The incineration process is capable of reducing the volume of waste entering the landfill by approximately 85%. But WtE isn’t just a trash disposal method. It’s a way torecover valuable resources: green energy but also ferrous, non-ferrous and precious metals. In fact, about 90% of metals contained in bottom ash can be recove-red while the remaining clinker can be reused as road material. For years, wet bottom ash handling has been the standard for WtE plants. Bottom ash (BA) produced by incineration process was discharged into a water bath for quenching and downstream handling in a wet state. However, a growing emphasis on environmentally - friendly issues is causing many plants to reconsider their production process – including ash handling - in order to comply with the stringent environmental regulations. As a result, dry bottom ash handling systems are replacing the polluting wet technology.
Magaldi has been the first company worldwide to introduce the dry bottom ash handling technology, using ambient air instead of water during the extraction and cooling phases. Specifically designed for WtE plants, the Ecobelt® WA (Waste Ash) system allows the dry removal of heterogeneous hot materials from grate boilers. By replacing water with air as primary cooling medium, the result is an effective environmental risk mitigation and a lower cost because there is no need to dispose of or treat water. Completely enclosed in a dust-proof steel casing to prevent any spillage of material into the environment, the Ecobelt® WA promotes an intimate contact between air and ash particles, that maximizes the cooling process and the unburnt carbon conversion. Ambient air enters the equipment through accurately sized inlet valves located along the conveyor while suitably designed skirtboards and special curtains/flaps hinged to the conveyor cover allow the ash passage whilst preventing uncontrolled air backflow to the furnace. Cooling air can be vented to the secondary air fan inlet and then injected into the combustion chamber so that a relevant amount of energy, mainly in the form of ash sensible heat, can be recovered to increase boiler efficiency. In addition, the Ecobelt® WA system increases the yields of the downstream metals recovery system, minimizing metals landfilling and providing high-quality raw materials. Since the incineration process cleans and separates metals from organic components, a dry extraction approach is the key factor to allow a more effective metal separation from inert matter. In fact, avoiding the reaction of bottom ash with water, metals can be recovered in their highest quality as well as in fine particle size (as 0.2 mm).
Units size: 2x54 MWth
Project type: Retrofit
Ash rate 1.6 t/h
Ash rate max: 10 t/h
Burned fuel: RDF
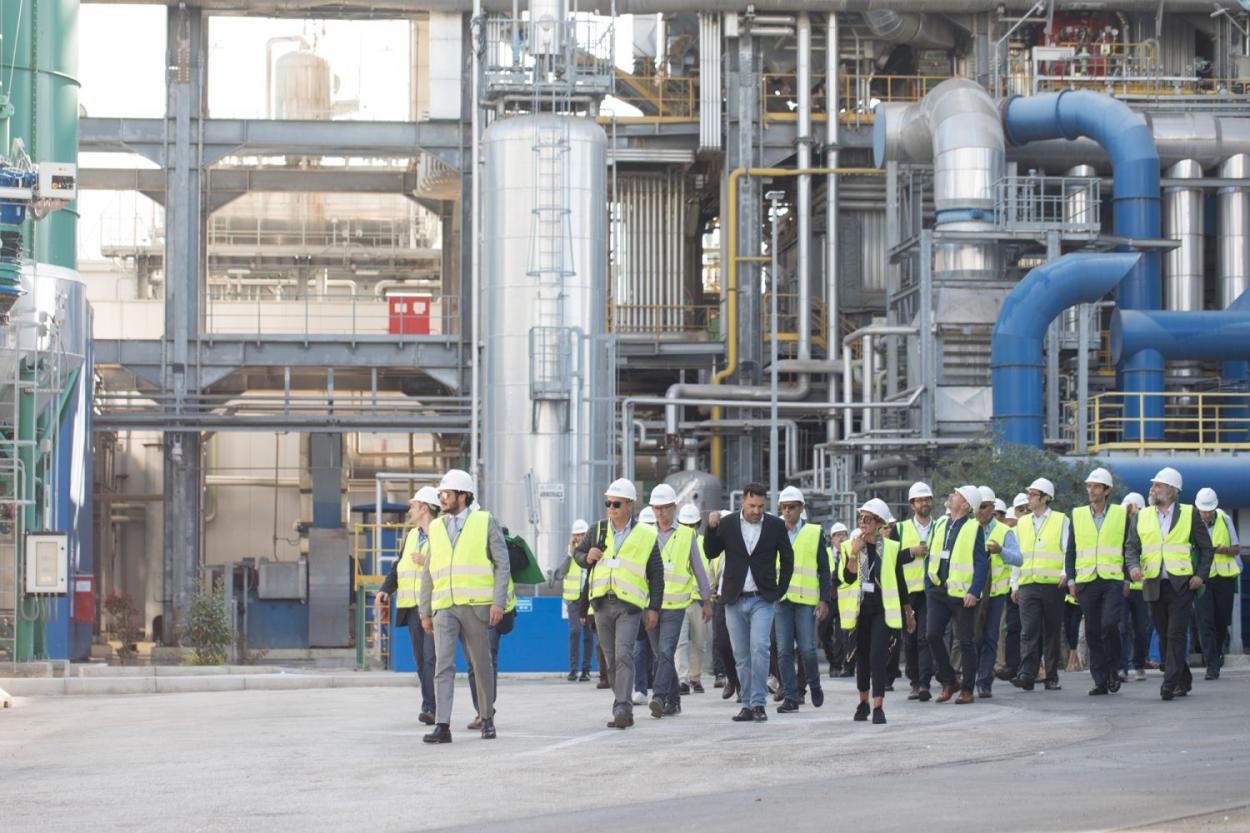
MAGALDI WTE OPEN DAY. THE EXPERIENCE OF SAN VITTORE DEL LAZIO WTE PLANT
Last October 2017, the Italian multi-utility Acea SpA open the door of its WtE plant in San Vittore del Lazio to the Magaldi WtE Open Day. The event hosted the main national and international players operating in the WtE business. More than 120 guests from major Italian firms (Herambiente, A2A, Iren Energia, Falck Renewables, among others), as well as international guests from Japan (Kawasaki Heavy Industries) to Azerbaijan (Tamiz Shahar JSC), from France (CNIM) to Germany (Doosan Lentjes GmbH), took part to the technical debate on the benefits provided by the dry system and, in particular, by the Ecobelt® WA technology. The decision to organize the event in San Vittore del Lazio was not accidental. Designed to thermally convert 397,200 tons per year of SSF (secondary solid fuel), the WtE plant is provided with 3x54 MWth combustion lines. Since 2016, the twin incineration lines #2 and #3 are equipped with the Magaldi dry technology. Magaldi realized the wet-to-dry conversion of the bottom ash handling system, replacing two submerged chain conveyors (SCC) handling wet ash from the discharge of the combustion grate to a temporary storage pit. The existing wet conveyors were causing serious problems. First of all, a large amount of waste had to be disposed due to the high percentage (>25%) of water in the slag/ash. Moreover, frequent clogging adversely affected the normal operation with consequent safety problems. Added to this, uncontrolled combustion and impossibility of carrying out maintenance with the system in operation. Using ambient air as cooling media, the Ecobelt® WA conveyors have allowed to eliminate the use of water to extract and cool both bottom ash and siftings thus cutting costs for ash/slag disposal and water treatment. Before the discharge into the pit, ash is conditioned by using a quantity of water <7.5% to keep dust down and allow a safe transportation to the treatment plant.