Enfriador MCC®
(Magaldi Casting Cooler)
Un sistema de alta ingeniería para gestionar de manera eficiente el transporte y el enfriamiento controlado de las piezas
Uno de los problemas de las fundiciones es la variabilidad ligada al tiempo de enfriamiento de las piezas. Este último puede variar según los volúmenes de producción, el tamaño de las piezas, los retrasos de las máquinas y otros factores incontrolables. Por lo tanto, un sistema de enfriamiento eficiente, como parte integral de un sistema de manejo de materiales diseñado correctamente, es fundamental para adaptarse a las necesidades específicas de producción y minimizar las variaciones de enfriamiento.
El transportador de enfriamiento MCC® ofrece un enfriamiento efectivo, alta eficiencia energética y no genera polvo.
Generalmente instalado entre la mesa sacudidora (shake-out) y la granalladora, el MCC® está compuesto por:
- el transportador Superbelt®, que es su componente clave.
El diseño multi-enlace de la malla asegura alta fiabilidad, bajo mantenimiento y operación continua sin problemas, evitando así costosas interrupciones. - Un túnel de enfriamiento en depresión.
Un flujo de aire ambiente entra por los extremos del túnel y sale por la compuerta de aspiración central. El aire de enfriamiento fluye a velocidad controlada sobre las piezas para enfriarlas hasta la temperatura deseada, evitando choques térmicos y/u otros defectos microestructurales.
Diseño robusto
Los transportadores de enfriamiento tienen que operar en condiciones adversas que incluyen arena, piezas abrasivas y altas temperaturas. Entornos como este requieren máquinas robustas que puedan compensar estas fluctuaciones.
Los transportadores de enfriamiento Magaldi están diseñados para resistir el desgaste de materiales extremadamente abrasivos y pueden soportar temperaturas más altas que cualquier otra tecnología competidora gracias al método patentado de conectar las placas a la malla metálica, que permite que todos lo elementos se expandan en cualquier dirección sin deformación permanente, mientras que el sistema de tensado compensa automáticamente las expansiones térmicas.
Proceso de enfriamiento diseñado
Para cada proyecto, Magaldi estudia minuciosamente las propiedades térmicas tanto del aire como de las piezas, para proporcionar el proceso de enfriamiento más eficiente.
El uso combinado de métodos analíticos (p. ej., análisis CFD), pruebas experimentales y mediciones de campo han hecho posible crear y probar modelos termodinámicos muy precisos, gracias a los cuales aseguramos modelos efectivos y, en última instancia, el proceso de enfriamiento.
Enfriamiento por aire controlado
Uno de los factores más críticos en el proceso de enfriamiento de las piezas es el método de intercambio de calor adoptado.
El transportador MCC® utiliza una combinación de flujos de aire paralelos y en contracorriente. El resultado es un gradiente de temperatura más bajo en la entrada del túnel, por lo que se reduce el estrés térmico en las piezas y se maximiza la eficiencia general del proceso de enfriamiento.
Enfriamiento eficiente incluso en espacios reducidos
En caso de limitaciones de espacio, es posible utilizar un flujo de aire adicional (flujo cruzado) que aumenta la eficacia del proceso de enfriamiento.
Con el transportador SuperMCC®, una tercera corriente de aire ingresa al sistema a través de orificios hechos en las placas de la banda. Ya que el aire de enfriamiento no solo fluye alrededor de las piezas, sino que también pasa por debajo y a través de ellas, una mayor parte de la superficie de la pieza está expuesta al aire y, por lo tanto, se enfría más rápido.
Sistema Integrado de Supervisión (MISS®)
Para obtener un proceso de enfriamiento fiable y flexible es necesario configurar y ajustar los parámetros de enfriamiento de las piezas. Por esta razón, los transportadores MCC® y SuperMCC® pueden equiparse con el sistema de supervisión integrado Magaldi (MISS®), que realiza un control dinámico de los parámetros del proceso según los diferentes tipos de pieza a manejar.
Conectado a las señales operativas de la línea de moldeo aguas arriba, el MISS® recibe el número de identificación (ID) de cada pieza y la temperatura real. De acuerdo con los parámetros indicados anteriormente, el MISS® ajusta automáticamente la velocidad de la cinta y el flujo de aire de enfriamiento, maximizando así tanto la productividad de la planta como la eficiencia del proceso de enfriamiento.
Emisiones reducidas de sílice cristalina
Los transportadores MCC® / SuperMCC® ofrecen una ventaja competitiva al tratar un problema muy apremiante en las fundiciones, es decir la exposición de los trabajadores al polvo de sílice cristalina. Gracias al transportador Superbelt®, que mueve las piezas sin vibraciones, la generación de polvo y la consiguiente exposición de los operadores se reducen significativamente.
Bajo consumo de energía
El transportador Superbelt® también permite reducir el consumo de energía (aprox. una décima parte en comparación con los transportadores vibratorios). Su diseño único evita la fricción por deslizamiento entre las partes móviles, minimizando así el desgaste y el consumo de energía para el proceso de transporte y enfriamiento.
"Todo en uno":
enfriamiento, desmazarotado y clasificación
Con el MCC® / SuperMCC®, la parte descubierta de la cinta aguas abajo del túnel de enfriamiento se puede utilizar como estación de trabajo para desmazarotar y clasificar las piezas, evitando la necesidad de máquinas adicionales. El transporte regualr y silencioso permite a los operadores clasificar las piezas cómodamente. Además, la banda es tan robusta que puede soportar las cargas de impacto generadas por las herramientas de desmazarotado (p. ej., martillos, cuñas hidráulicas, manipuladores, robots).
Algunas historias de éxito
Slovenia
Raffreddamento fusioni
Fonderia di ghisa
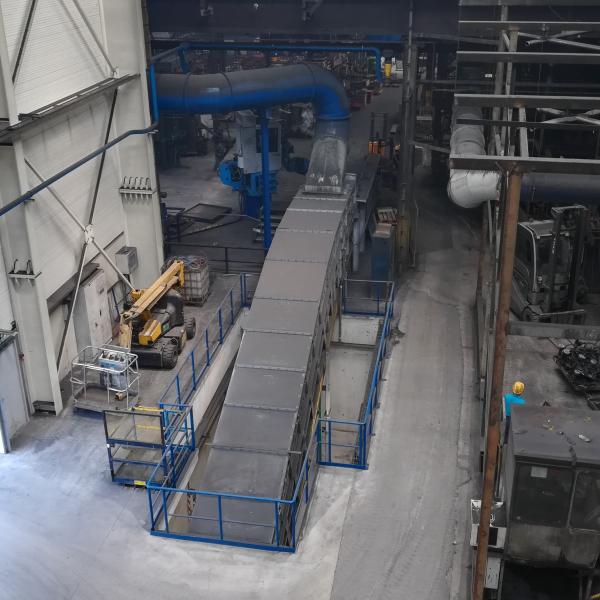
Controllo ottimale dei parametri di raffreddamento grazie al sistema MISS®
Il Cliente
Azienda leader nella produzione di componenti in ghisa sferoidale e grigia per l’industria ferroviaria.
La Sfida
L'obiettivo per la fonderia era raffreddare fusioni di grandi dimensioni e peso elevato, caratterizzate da alte temperature e un alto modulo termico.
La Soluzione
Gli ingegneri Magaldi hanno condotto test specifici per validare le curve di raffreddamento ottenute con codici di simulazione proprietari. Il risultato è stato un trasportatore MCC® in grado di raffreddare fusioni pesanti (fino a 633 kg) e di grandi dimensioni provenienti dalla linea di scuotimento a forma di “L”, portandole da 700°C a 70°C.
Italia
Raffreddamento fusioni
Fonderia di ghisa
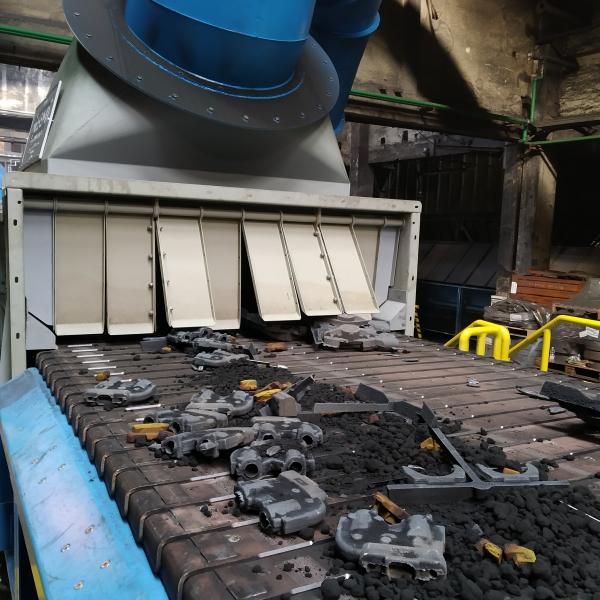
Processo di raffreddamento controllato per produzioni ad alto volume.
Il Cliente
La fonderia produce getti in ghisa grigia e sferoidale per diversi settori industriali.
La Sfida
Nell'ambito di un progetto di ammodernamento delle linee verticali DISA, il Cliente si è rivolto alla Magaldi alla ricerca di una soluzione integrata per il raffreddamento e la smaterozzatura dei getti che dalla zona di distaffatura sono trasferiti alla granigliatrice.
La Soluzione
Dopo la fase di distaffatura/sterratura, 2 trasportatori vibranti scaricano i getti sul raffreddatore Magaldi disposto ortogonalmente.
Il lungo MCC® raffredda le fusioni in sincrono con le linee DISA a monte. All'uscita del tunnel di raffreddamento, gli operatori eseguono la cernita e la smaterozzatura dei getti sul tratto scoperto del nastro. Le materozze vengono, invece, scaricate in un sistema automatico di movimentazione dei cassoni posto in testata di trazione per il successivo trasferimento all'area di fusione.
P.R.C.
Enfriamiento de piezas
Fundición de hierro

El MCC® redujo las tasas de desechos y maximizó la calidad del producto a través de un proceso de enfriamiento de aire personalizado.
El Cliente
Fundición moderna especializada en la producción de bloques de motor de hierro fundido.
El Reto
Aumentar la calidad de las piezas fundidas mejorando el rendimiento y la eficacia del sistema de enfriamiento.
La Solución
Aguas abajo de las shakeouts, 2 canales vibratorios recogen las piezas y las descargan en los enfriadores MCC® formando un solo túnel de enfriamiento de 54 m de largo. En el interior del túnel, un flujo continuo de 40 t/h de piezas se lleva desde una temperatura de 450°C a 80°C. A la salida del túnel, la parte descubierta de la cinta se utiliza como estación de trabajo para clasificar y desmazarotar las piezas mediante manipuladores.