Magaldi Casting Cooler
(MCC®)
Un système hautement avancé pour bien gérer le transport sécurisé et le refroidissement régulé des pièces moulées
L’efficacité du processus de refroidissement, qui est affecté par le temps de séjour des pièces à l’intérieur du tunnel de refroidissement, est l’un des principaux défis à relever pour obtenir pièces moulées de haute qualité.
Le temps de refroidissement peut varier en fonction des volumes de production, de la taille des pièces moulées, de l’espace disponible ainsi que d’autres facteurs imprévisibles. Pour une production réussie, il est indispensable de disposer d’un système flexible permettant de maîtriser le processus de refroidissement et de s’adapter aux besoins spécifiques de la production.
Le MCC® est généralement installé entre la décocheuse et la sableuse. Il se compose de :
- Le convoyeur Superbelt® comme composant clé: La conception multi-lien de la bande, qui garantit la redondance, permet d’obtenir un convoyeur qui non seulement nécessite un entretien minimal ou inexistant, mais qui fonctionne aussi en continu et sans imprévus, ce qui évite d’onéreuses interruptions de production.
- Un tunnel de refroidissement maintenu à pression négative: L’air ambiant est aspiré par les extrémités du tunnel de refroidissement et sort par la hotte centrale. L’air de refroidissement à vitesse régulée circule sur les pièces moulées, les refroidissant à la température souhaitée sans provoquer de chocs thermiques ou d’autres défauts microstructuraux.
Une conception robuste
Fonctionnant dans des conditions difficiles, les convoyeurs de refroidissement de pièces moulées doivent résister à l’abrasion des pièces et du sable ainsi qu’à des températures extrêmes. Pour relever ces défis, il est indispensable d’utiliser des machines robustes.
Le convoyeur MCC® est réputé pour sa grande résistance à l’abrasion, même à des températures de fonctionnement élevées. L’assemblage particulier des écailles à la bande maillée permet à tous les composants de se dilater dans n’importe quelle direction sans provoquer de dommages permanents tandis que le dispositif de mise en tension compose automatiquement les dilatations thermiques.
Un processus conçu sur mesure pour le refroidissement
Pour chaque projet, Magaldi étudie méticuleusement les propriétés thermiques à la fois de l’air et des pièces moulées afin de garantir un processus de refroidissement aussi performant que possible. En s’appuyant à la fois sur des méthodes analytiques (analyse CFD), des tests expérimentaux sur son banc d’essai en interne et des mesures prises sur le terrain, l’entreprise parvient à obtenir des modèles thermodynamiques d’une grande précision. Cette approche garantit une modélisation efficace et, par conséquent, un processus de refroidissement très performant.
Refroidissement par air régulé
La méthode d’échange de chaleur adoptée en vue du refroidissement représente l’un des facteurs les plus critiques du processus de refroidissement des pièces moulées.
Le convoyeur MCC® utilise à la fois des flux d’air à co-courant et à contre-courant. Il en résulte un gradient de température plus faible à l’entrée du tunnel de refroidissement permettant de réduire les contraintes thermiques des pièces moulées tout en maximisant l’efficacité globale du processus de refroidissement.
Une structure compacte
Le convoyeur SuperMCC® se distingue par un troisième flux d’air (flux transversal) qui pénètre dans le système via des fentes spécialement prévues à cet effet dans les écailles de la bande. Le fait que l’air de refroidissement circule non seulement autour des pièces moulées mais passe également en dessous et à travers permet d’exposer une plus grande partie de la surface des pièces, gage d’un meilleur refroidissement et d’un moindre encombrement de l’équipement. Cette solution est ainsi idéale dans les environnements disposant de peu de place.
Système MISS® (Magaldi Integrated Supervision System)
Pour assurer un processus fiable et flexible, il est indispensable de garantir un réglage de précision et un bon ajustement des paramètres de refroidissement des pièces moulées. C’est la raison pour laquelle les convoyeurs MCC® peuvent être équipés du système MISS® (Magaldi Integrated Supervision System) qui effectue un contrôle dynamique des paramètres du processus en fonction des différents types de pièces moulées à convoyer.
Connecté aux signaux opérationnels de la ligne de moulage, le MISS® reçoit le numéro d’identification de chaque pièce moulée ainsi que sa température réelle. En fonction des paramètres ci-dessus, il ajuste automatiquement la vitesse de la bande et le débit de l’air de refroidissement, maximisant ainsi à la fois la productivité de l’installation et du processus de refroidissement.
Réduction des émissions de poussière de silice
Les systèmes MCC®/SuperMCC® offrent un avantage concurrentiel majeur en ce qui concerne un problème hautement sensible, à savoir l’exposition des travailleurs à la poussière de silice cristalline.
La simplicité de fonctionnement du système de convoyage de Magaldi garantit un transport sans à-coups et sans vibrations qui permet de minimiser les émissions de poussière, favorisant ainsi un environnement de travail plus sûr et plus sain.
Faible consommation d’énergie
Le convoyeur Superbelt® se distingue par sa faible consommation d'énergie (environ un dixième par rapport aux convoyeurs vibrants ou aux tambours de refroidissement). Spécialement conçu pour éviter les frottements de glissement entre les pièces mobiles, le convoyeur minimise à la fois l’usure et la consommation d’énergie du processus de transport et de refroidissement.
"Tout en un":
refroidissement, dégagement et tri
Avec le MCC®/le SuperMCC®, la longueur non couverte de la bande en aval du tunnel de refroidissement peut être utilisée comme poste de travail pour la découpe des systèmes d’alimentation et le triage des pièces moulées, ce qui permet d’éviter le recours à d’autres équipements. Le transport silencieux et sans à-coups permet aux opérateurs de trier confortablement les pièces moulées. De plus, la bande est suffisamment robuste pour résister aux impacts provenant des outils de découpe des systèmes d’alimentation (notamment marteaux, cales hydrauliques, manipulateurs et robots).
Quelques projets réalisés
Slovénie
Refroidissement des moulages
Fonderie de fer
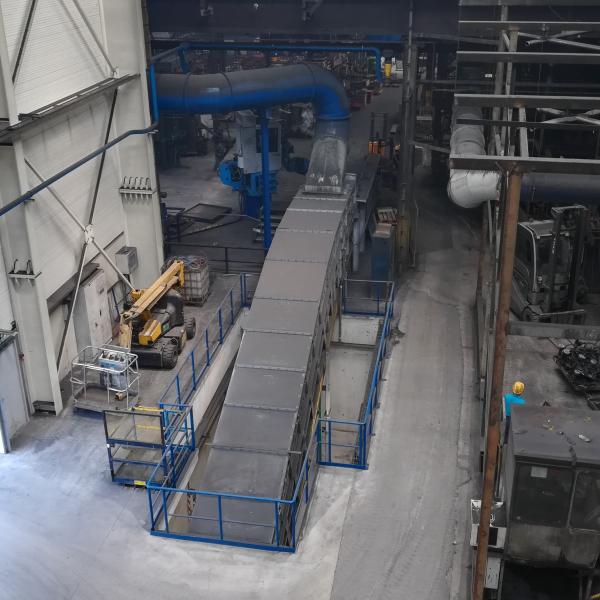
Contrôle optimal des paramètres de refroidissement grâce au système MISS®
Le Client
Chef fabricant de composants en fonte ductile et grise pour l'industrie ferroviaire.
Le Défi
L'objectif de la fonderie était de refroidir d'énormes et lourds moulages présentant des températures élevées et un module thermique élevé.
La Solution
Les ingénieurs de Magaldi ont réalisé des bancs d'essai dédiés pour valider les courbes de refroidissement obtenues avec des codes de simulation propriétaires. Le résultat a été un convoyeur MCC® capable de refroidir les lourds moulages (jusqu'à 633 kg) et de grande taille provenant de la ligne de décochage en forme de “L”, en passant de 700°C à 70°C.
Italie
Refroidissement des moulages
Fonderie de fer
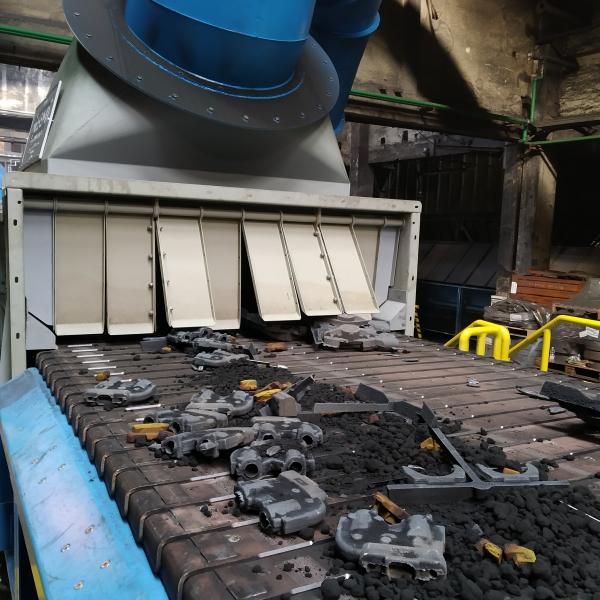
Processus de refroidissement contrôlé pour les productions à grand volume.
Le Client
La fonderie produit des pièces en fonte grise et en fonte ductile pour divers secteurs industriels.
Le Défi
Dans le cadre d’un projet de modernisation des lignes verticales DISA, le Client s’est adressé à Magaldi pour une solution intégrée de refroidissement et d’ébavurage des pièces, transférées de la zone de décochage à la grenailleuse.
La Solution
Après la phase de décochage/dessablage, deux convoyeurs vibrants déversent les pièces sur le refroidisseur Magaldi disposé orthogonalement. Le long MCC® refroidit les moulages en synchronisation avec les lignes DISA en amont. À la sortie du tunnel de refroidissement, les opérateurs effectuent le tri et l’ébavurage des pièces sur la partie découverte du convoyeur. Les masselottes, quant à elles, sont évacuées vers un système automatique de manutention des bennes situé en tête de traction, pour être ensuite transférées vers la zone de fusion.
P.R.C.
Refroidissement des moulages
Fonderie de fonte

Avec l’installation du refroidisseur Magaldi, le client a réduit le taux de rebut des moulages et amélioré la qualité du produit fini.
The Customer
Fonderie moderne spécialisée dans la production de blocs-moteurs en fonte.
Le Défi
Améliorer la qualité des moulages en optimisant les performances et l’efficacité du système de refroidissement.
La Solution
En aval des décochages, deux canaux vibrants collectent les moulages et les déversent sur les refroidisseurs MCC®, formant un tunnel de refroidissement unique de 54 m de long. À l’intérieur du tunnel, un flux continu de 40 t/h de pièces est refroidi de 450°C à 80°C. À la sortie du tunnel, la partie découverte du convoyeur sert de poste de travail pour le tri et l’ébavurage des moulages à l’aide de manipulateurs.