Convoyeur Ecobelt®
Réduction de la durée du cycle de convoyage des matériaux ainsi que de la chute de température des matériaux transportés en vue d’un processus de refusion en aval plus efficace et plus rentable.
La fusion de l’aluminium secondaire transforme les rebuts d’aluminium en aluminium utilisable et recyclable à de multiples reprises grâce à un processus en boucle fermée.
Ce processus présente d’importants avantages écologiques et économiques en termes de réduction des déchets en décharge, d’émissions de gaz à effet de serre et de consommation d’énergie (recycler une tonne d’aluminium ne nécessite que 5 % de l’énergie utilisée pour raffiner l’aluminium primaire à partir du minerai de bauxite), ce qui fait de l’aluminium secondaire un matériau respectueux de l’environnement et économiquement viable.
Dans la mesure où les rebuts d’aluminium proviennent de différentes sources, la présence d’impuretés nécessite des opérations et des traitements préliminaires (notamment triage, fragmentation et traitements thermiques) pour améliorer leur qualité en termes de rendement en métal et de recyclabilité.
La possibilité de décaper l’aluminium, généralement au moyen d’un four rotatif, améliore en particulier le processus en réduisant les pertes de métal et en permettant l’utilisation d’une plus large gamme de rebuts.
Magaldi a adapté sa technologie de convoyage afin de prendre en charge le processus de décapage. Son convoyeur Ecobelt® a ainsi été conçu pour transporter des broyats chauds depuis le four de décapage vers le four de fusion. Dans les installations disposant de plusieurs fours, le système intégré de détection des débits détermine le débit total partagé et le répartit entre chaque four au moyen d’une vanne de dérivation spécialement prévue à cet effet.
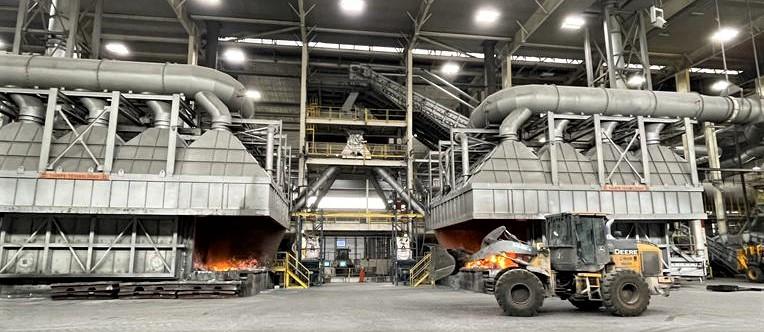
Haute fiabilité
Le convoyeur Ecobelt® est doté d’écailles en acier partiellement superposées et solidement boulonnées sur un système breveté à maille à double fil.
Les écailles sont équipées de taquets transversaux qui permettent de maintenir les matériaux sur la bande lors de leur convoyage sur des pentes.
En raison de sa conception multi-lien, la bande est ultra-résistante. La maille assure la redondance, un entretien minimal ou inexistant et un fonctionnement continu sans obstacles. Même si la maille est gravement endommagée, le convoyeur continuera à fonctionner sans défaillances soudaines jusqu’à l’arrêt prévu pour la maintenance programmée.
Garantissant productivité et rentabilité, le fonctionnement sans imprévus se traduit par des gains d’efficacité et de disponibilité, ceci 24 heures sur 24, 7 jours sur 7, toute l’année.
Résistance à haute température
La température des broyats au point de déchargement du four est de l’ordre de 500 à 600 °C. Il est donc primordial d’utiliser un convoyeur résistant à la chaleur pour garantir la sécurité et la fiabilité du transport.
Grâce à une méthode brevetée d’assemblage des écailles à la bande maillée permettant à tous les éléments de se dilater librement dans n’importe quelle direction sans provoquer de déformations permanentes, le convoyeur Ecobelt® résout les problèmes posés par les hautes températures et les déchirures. Le convoyeur est ainsi capable de résister à des températures allant jusqu’à 1100 °C.
Réduction des émissions de poussière et
faible chute de température
Entièrement fermé dans une enveloppe en acier minimisant les émissions de poussière, le convoyeur Ecobelt® garantit une chute de température des matériaux transportés aussi faible que possible. Cela signifie qu’il est possible de charger des broyats d’aluminium dans le four de fusion alors qu’ils sont encore chauds, ce qui permet de réduire le temps de fusion requis et ainsi d’économiser de l’énergie.
Fonctionnement très silencieux
Le fonctionnement sans à-coups et sans vibrations du convoyeur Ecobelt® ainsi que sa structure entièrement fermée réduisent considérablement les émissions sonores.
Le niveau sonore d’Ecobelt® est généralement inférieur à 75 dB(A), soit moitié moins que celui des convoyeurs à chaînes traditionnels.
Maintenance facile et nécessitant peu d’interventions
Le remplacement des systèmes de convoyage classiques par des convoyeurs Ecobelt® est toujours synonyme de réduction des temps d’arrêt et des coûts de maintenance.
L’absence de chaînes, de pignons, de barres d’usure et de roues dentées diminue considérablement à la fois le taux d’usure du convoyeur à bande et les coûts d’exploitation et de maintenance qui lui sont liés.
De plus, compte tenu que le temps de disponibilité est un facteur critique pour tous les convoyeurs, l’Ecobelt® a été conçu pour permettre un remplacement rapide des composants clés malgré la structure fermée. Tous les roulements sont installés sur l’extérieur de l’enveloppe, à un endroit propre et froid, ce qui permet une maintenance facile et une lubrification pendant le fonctionnement de la bande.
Quelques projets réalisés
Allemagne
Transport de broyats chauds
Usine de recyclage d'aluminium
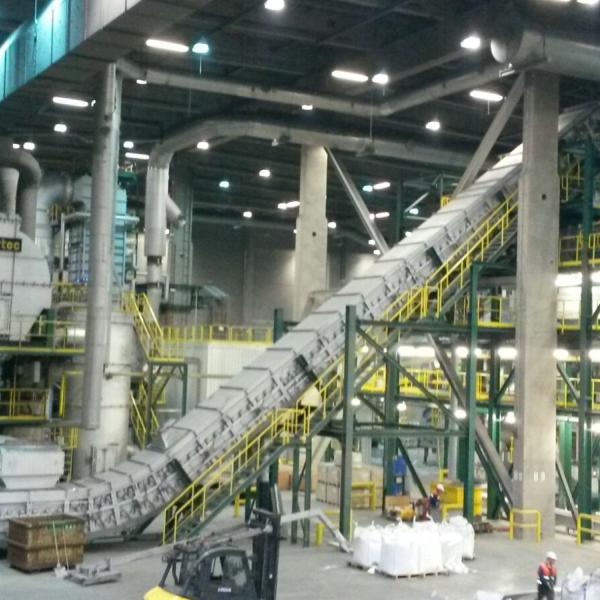
Grâce à leur étanchéité améliorée, les convoyeurs Ecobelt® réduisent considérablement les pertes de chaleur. L'énergie thermique libérée par les processus en amont est réutilisée dans le fusion.
Le client
Le centre de recyclage d’aluminium le plus grand et le plus avancé au monde sur le plan technologique traite jusqu’à 400 000 tonnes de ferraille par an.
Le défi
Les convoyeurs à tablier utilisés pour transporter les broyats chauds des délaiseurs rotatifs vers les fours de fusion nécessitaient une maintenance extrêmement lourde, car les bagues et les maillons de chaîne - directement exposés à des températures élevées et à des matériaux poussiéreux - devaient être fréquemment graissés. En outre, les convoyeurs existants provoquaient une dispersion importante de la chaleur, et les pertes de chaleur qui en résultaient rendaient le processus moins efficace. Le client devait absolument trouver une solution plus fiable.
La solution
Magaldi a accepté de simuler les conditions d'exploitation de l'usine pour mieux adapter la solution. Huit convoyeurs Ecobelt® desservent les lignes Can et Flex et transportent les broyats chauds (550°C) des fours rotatifs vers les fours de fusion en aval. Les convoyeurs fonctionnent en trois équipes, à des températures élevées et dans des conditions sévères, garantissant une fiabilité de 98 % et la plus faible chute de température possible.
États-Unis
Transport de broyats chauds
Usine de recyclage d'aluminium

Les efforts de maintenance ont été réduits. L'usine doit ainsi faire face à moins de dépenses d'exploitation et à des temps d'arrêt réduits.
Le client
Usine de recyclage d'aluminium spécialisée dans la fabrication de tôles d'aluminium laminées à plat pour le marché des canettes de boissons.
Le défi
L'installation était en proie à une série de pannes. La tentative d'utiliser un convoyeur à tablier pour transporter les broyats chauds s'est avérée infructueuse en raison des arrêts fréquents pour réparer les chaînes cassées.
La solution
Quatre convoyeurs Ecobelt® ont été installés pour relier les fours de délaquage aux fours en aval, transportant jusqu'à 20 t/h de copeaux d'aluminium à une température d'environ 580 °C. Contrairement aux convoyeurs à tablier, l'Ecobelt® garantit une disponibilité et une fiabilité élevées, offrant une plus grande assurance de temps de fonctionnement et une réduction de la maintenance. En outre, la réduction de la chute de température a eu un effet positif sur les performances des fours en aval, en réduisant la consommation d'énergie.