The Ecobelt® B conveyor
The ideal solution for safe and spillage-free transportation of hot sand
Hot sand conveying is still a prominent problem facing green sand foundries.
Conventional methods (rubber belts, vibratory conveyors, coolers/classifiers + pneumatic transport) used to handle hot sand have proven to suffer from high O&M costs due to high temperatures and wear issues caused by the sand composition with sharp and hard foreign particles.
Additionally, the potential for a huge amount of fugitive dust during this type of material handling causes serious health concerns for employees and a decrease in the overall efficiency of operations.
The Ecobelt® B bucket conveyor has been designed to handle hot, very fine, dusty, and abrasive bulk materials, with significantly high inclinations. All issues related to high temperatures, premature wear, and silica dust emissions are fully eliminated in favor of smooth, reliable, and environmentally friendly transport.
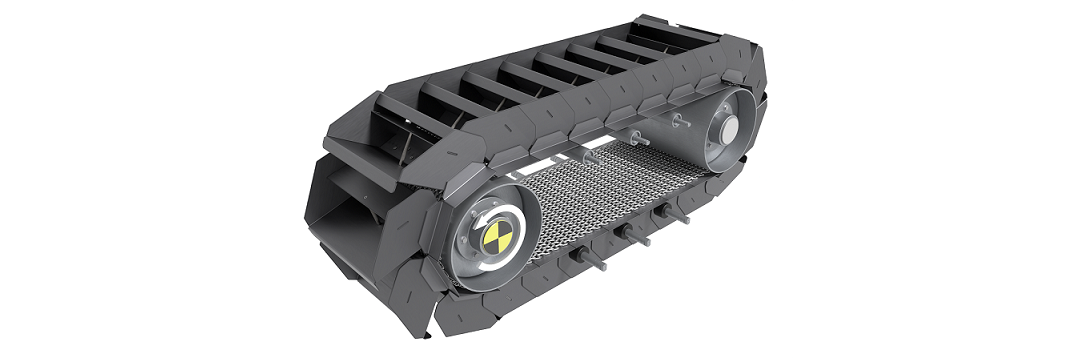
High reliability
The Ecobelt® B conveyor is made up of the assembly of a series of buckets, whose thickness and steel quality are selected according to the required capacity and the type of material to convey, onto a high-tensile mesh.
The belt design is based on a multi-link concept which ensures trouble-free operation, eliminating any risk of sudden failure. Even in the event the mesh is severely damaged, the conveyor will keep running till the scheduled maintenance.
The unmatched reliability also results in high availability during 24/7, year-round operation.
High conveying capacities and steep inclines
Buckets meet all requirements typically encountered in the case of sand transportation, including high conveying capacities and steep inclines.
The first requirement is achieved because buckets – which can be designed up to 1,600 mm wide - maximize area by their unique interlocking design, allowing for increased transportation.
The Ecobelt® B has also proven reliability for transporting bulk materials across steep inclinations (up to 75°), avoiding the material from roll-back (usually occurring when the conveyor slope exceeds 18/22°).
High temperature resistance
Heat is widely recognized as the most unforgiving and damaging factor for conveying technologies.
As foundry sand can reach temperatures above 150 °C downstream the shakeout, the conveying equipment must be heat resistant.
Rubber belt conveyors have proven to be extremely expensive in terms of operating costs as hot sand can cause burns and sudden failure of the belt, which needs to be changed more and more often.
The Ecobelt® B conveyor has been designed to withstand temperatures higher than any other competing technology. The patented method of connecting the buckets to the mesh belt leaves all components to freely expand in any direction without permanent deformations while the take-up device automatically compensates for thermal expansions.
Reduced silica dust emissions
Foundry sand conveying can lead to the generation of fugitive dust and respirable crystalline silica.
With vibratory conveyors, dust containment turns from a major concern into a real nightmare. Due to the concept design based on vibrations and shaking, vibratory equipment has a huge potential to spill large volumes of dust into the air, making it difficult to prevent silica exposure. Continuing to rely on vibratory equipment for hot sand conveying may no longer be an option.
With the Ecobelt® B conveyor, dust emissions are significantly reduced. The gentle and smooth transport, along with the fully enclosed environment, greatly reduces fines generation and employee exposure to dust and silica.
Reduced maintenance requirements
& negligible wear
Minimizing maintenance costs ranks near the top priority when planning foundry equipment investments. That is why pneumatic conveying systems are definitely not a good choice for moving sand. They suffer from fast erosive wear of bends and pipes so operating and maintenance costs are very high.
With the Ecobelt® B conveyor, because there is no relative motion between conveyed material and steel parts during transportation, wear is drastically reduced, and O&M costs are slashed to the bone due to the absence of wear bars or sprockets.
Additionally, the casing does not affect the maintainability: all idler supports are installed outside, allowing for trouble-free inspection at any time and lubrication with the belt in operation.
Some successful stories
USA
Rotary drum infeed
Steel foundry
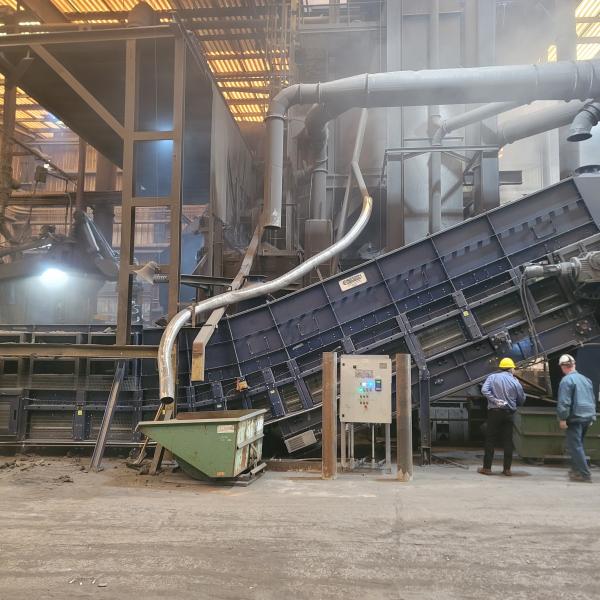
A cost-effective, high-value conveying technology for sand transfer.
The Customer
Captive steel foundry in Pulaski (TN)
The Challenge
The existing vibratory conveyor handled green sand, which was separated from castings and sprues via a manipulator, while molds were transported on a shake-out conveyor. Sand from the shake-out was conveyed at a 90° angle and dropped into the lower infeed conveyor. The sand was eventually discharged into a rotary drum, where the big chunks were broken, and tramp metal was recovered before sand reclamation.
The existing infeed conveyor was badly worn-out, required high maintenance costs to keep it running, and continuously spread sand in the surrounding environment. That’s why the foundry management opted for a change of technology, selecting the Magaldi conveyor to improve operations and the cleanness of the area.
The Solution
In close cooperation with the Customer, Magaldi has been able to design a solution to fit in the same space occupied by the vibratory infeed conveyor, with only minor modifications to the existing structures.
The Ecobelt® gently conveys the sand discharged from the shake-out, and any residual metal tramp, up to the drum, solving all operational problems caused by the existing vibratory infeed conveyor. Installed HP is lowered by 70%, silica emissions are drastically reduced, and O&M costs are offset thanks to the special design of the belt which ensures a long-lasting life span.
P.R.C.
Hot sand conveying
Iron foundry
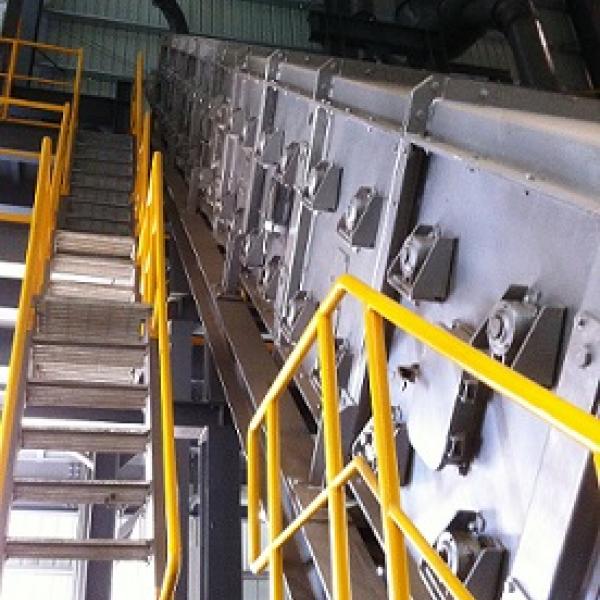
The Ecobelt® conveyor proved to be ideal for installations with space constraints because of its ability to tackle steep inclinations.
The Customer
Manufacturer of fully machined cast iron and steel products for the mining industry.
The Challenge
The foundry was in need of a hot chemical sand conveyor able to fit in the tight available space.
The Solution
Magaldi carried out field measurements and conceptual drawings to ensure the conveyor could fit in the confined space. Finally, an Ecobelt® conveyor – equipped with the automatic sand recovery system O-chain® - was installed underneath the shake-outs to continuously move 80 t/h of hot sand at 400°C up to the cooling system.
The Ecobelt® not only met the space constraints thanks to its capability to ramp up across steep inclinations but also eliminated any possible leaks down the road.
USA
Hot sand conveying
Iron foundry

The Ecobelt® conveyor improved the safety and quality of the working environment.
The Customer
Foundry specialized in large industrial castings for sophisticated mining equipment.
The Challenge
To safely convey hot chemical sand.
The Solution
Installed underneath the shake-out, the Ecobelt® conveyor moves 50 t/h of hot sand (315°C) up to the downstream cooling drum. The reduction in dust spillage and environmental hazards significantly improved worker safety.