Superbelt® conveyors
Gentle and smooth transport of cast parts
Smooth handling is often a major factor in assuring casting quality and secure productivity.
The Superbelt® conveyor is the recommended solution for the gentle and smooth transport of cast parts throughout the plant. It can be integrated into complex conveying processes and ensure continuous conveying performance while moving castings of different dimensions, shapes, and weights, for short or long paths, straight or inclined.
High reliability
The Superbelt® conveyor is made up of partially overlapping steel pans securely bolted on a patented steel double-wire mesh system.
The belt design is based on a multi-link concept that ensures redundancy, little to no maintenance, and trouble-free continuous operation. Even if the mesh is severely damaged, the conveyor will keep on running till the scheduled maintenance, without sudden failures.
The trouble-free operation allows to preserve the productivity and profitability of the whole plant and results in greater efficiency and uptime during 24/7, year-round operation.
High temperature resistance
The patented method of connecting the pans to the mesh belt leaves all components to freely expand in any direction without permanent deformations. The take-up device automatically compensates for thermal expansions.
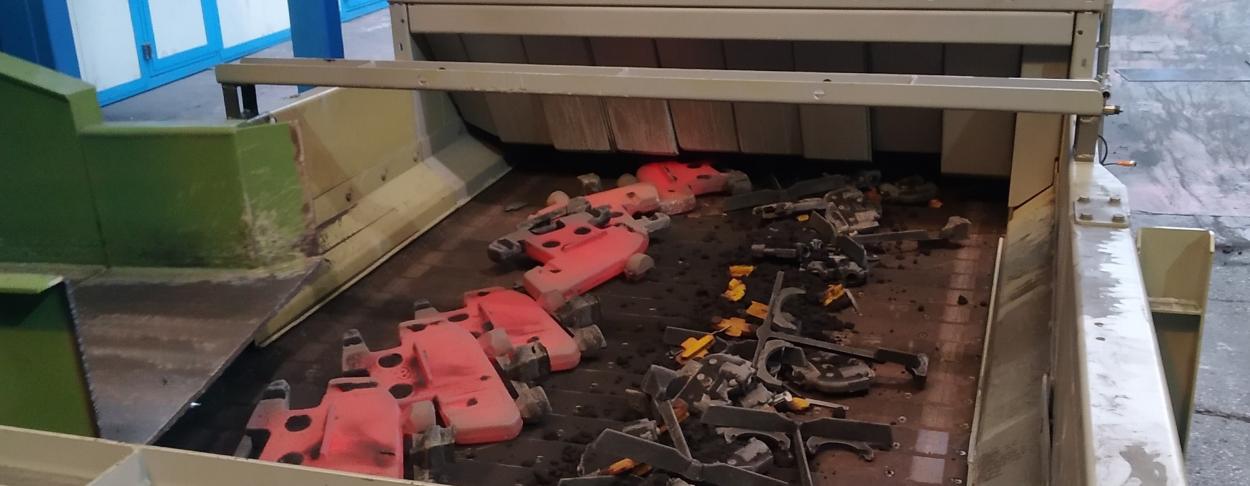
Reduced silica dust emissions
The Superbelt® conveyor provides a competitive edge in dealing with a highly sensitive issue, namely workers' exposure to crystalline silica dust.
The simple operation of the Magaldi conveyor system ensures smooth running without vibrations which, in turn, minimizes dust emissions, contributing to a safer and healthier work environment.
Low energy consumption
Designed to avoid sliding friction among the moving parts, the Superbelt® conveyor requires a very low power demand (generally about one-tenth of vibratory conveyors).
The amount of energy savings also depends on the length of the belt. As such, with the Superbelt®, the longer the conveyor is, the greater the energy savings are.
Unique discharge chute for
reduced damage to cast parts
Castings can be not only hot but also extremely delicate to handle.
Smooth running is key to reducing the risk of damaging cast parts during transport.
To preserve the quality of thin-walled castings even during the transfer stage, Magaldi designed, developed, and tested a new discharge chute featuring a unique “sandwich” design that reduces both the shock impact loads and the resulting noise.
Negligible wear
With the Superbelt® conveyor, wear is negligible since the material is slowly conveyed with no relative motion against steel parts.
Additionally, the conveyor runs on smooth sealed idlers with bearings (no wear bars).
Low maintenance requirements
The Superbelt® conveyor requires little to no maintenance as it is devoid of critical wear points (no wear bars, pins, hinges, chains, or sprockets). The only points requiring lubrication are the bearings of the head and tail pulley, which can be greased with the belt in operation. The other components are designed for continuous operation and can be checked during preventive maintenance over a multi-year schedule.
Some successful stories
Poland
Casting conveying
Iron foundry
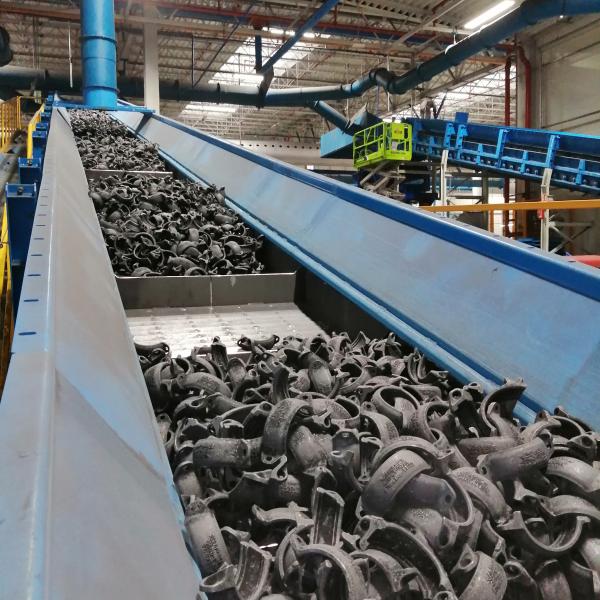
Unmatched ability to convey castings across steep inclinations
The Customer
Global manufacturer of valve and pipe products. The iron foundry in Poland is one of the most modern in Europe, specialized in manufacturing castings weighing 2-25 lb for OEM's and automotive suppliers.
The Challenge
The Customer was looking for a solution to convey special fittings across a steep inclination.
The Solution
Magaldi installed 2 Superbelt® conveyors downstream of the molding lines to move castings from the de-gating and sorting area up to the shot-blasting machine. The conveyors are equipped with:
- cleats on the pans to receive and transport a specific volume of material in start&stop mode;
- an encoder to pinpoint the exact position.