The MAP® system
(Magaldi Ash Postcombustor)
A patented system for enhancing and controlling the unburned carbon (UBC) post-combustion process on the steel belt conveyor
In case of co-combustion (coal + biomass/RDF) or PCF boilers burning solid fuels with milling difficulties (e.g. lignite, coal boilers converted to 100% RDF or biomass), the MAP® system allows carrying on the combustion process of unburnt residues on the steel belt.
Dry vs. Wet
Unlike conventional wet bottom ash handling (WBAH) systems, responsible for huge water consumption, particles and fines floating in the water bath, high maintenance costs, environmental issues, and negative effects on boiler operation, the MAP® system delivers a reliable, cost-effective, and environmentally friendly operation thanks to the unique combination of the dry cooling process and the dependable Superbelt® conveying technology.
Water & related cost savings
The use of the dry bottom ash handling system results in significant water and O&M cost savings. Since no water is used for bottom ash cooling and conveying, pumps, piping, and water treatment systems are no longer necessary, and the associated costs are eliminated.
Based on the specific project needs, a minimum water flow can be used to reduce dust dispersion at the discharge point. The water rate can be controlled and set during operation.
Enhanced & controlled post-combustion
The main advantage of implementing the MAP® system is the enhanced oxidation of unburned carbon (UBC) in dry bottom ash. It achieves the greatest benefits whereas the coarser fuel (d > 1.0÷2.0 mm) does not have a residence time in the combustion chamber long enough to burn completely.
Due to the furnace's negative pressure, the ambient air enters the casing of the MAP® extractor and surrounds the ash particles on the conveyor. UBC oxidation is also supported and promoted by the flame radiation through the boiler throat.
The temperature inside the system is continuously monitored, and the hot flow is adjusted to keep the process parameters and O2 concentration under control.
Therefore, the UBC residual content in bottom ash is minimized, increasing its potential for sale or easier disposal.
Increase in boiler efficiency &
environmental risks mitigation
The MAP® dry bottom ash handling system allows for a significant increase in boiler efficiency.
Ash cooling begins right after the post-combustion zone, using added ambient air. As a result, cooling and post-combustion airflows enter the boiler throat at quite a high temperature, recovering a significant amount of energy in the form of ash sensible heat, ash chemical energy from unburnt particles, and boiler radiation flux through the throat.
The resulting increase in boiler efficiency leads to less fuel consumption which, in turn, reduces CO2 emissions and ensures effective environmental risk mitigation.
Potential increase in maximum co-fuel particle size
In power plants operated under co-firing conditions, the co-fuel feed particle size may adversely affect the combustion process since coarse biomass/RDF particles tend to fall from the feeding points together with bottom ash, thus increasing the carbon-in-ash levels.
As integrated with the boiler, the MAP® system reduces the restrictions on the co-fuel size distribution and mixing conditions. By allowing for post-combustion on the conveyor belt, there is no need to grind biomass/RDF, which is an expensive and energy-intensive process. Hence, the potential increase in maximum co-fuel particle size reduces the capital cost for the co-fuel screening and pulverizing system.
Reduced disposal costs &
Increased ash marketability
The implementation of the MAP® dry bottom ash handling system greatly reduces ash disposal costs. The absence of water cuts the costs for landfilling due to a significant reduction in ash weight.
As a gainful alternative to landfilling, bottom ash can be sold to the cement industry since its features (dry and with lower unburned content) increase its saleability.
The Superbelt® conveyor technology
Apart from the overall benefits of dry over the wet system, the MAR® system offers compelling benefits that derive from the use of the Superbelt® conveyor applied to dry ash handling, including:
- high dependability
- high temperature resistance
- high resistance to impact
- negligible wear and no tear issues
- low power demand
- low and easy maintenance.
Some successful stories
Romania
Post-combustion of high UBC bottom ash
Coal-fired power plant
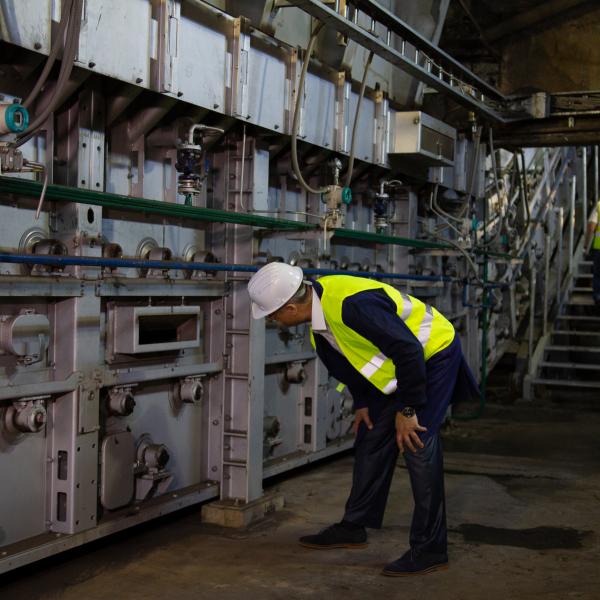
The MAP® system allowed achieving a reduction in UBC content ranging from 15 to 40%. This increased boiler efficiency by 2÷4% (depending on operating conditions) and resulted in a significant reduction in CO2 emissions.
The Customer
Large lignite-fired thermal power plant (3x315 MWe)
The Challenge
Driven by the need to modernize the plant, the Customer decided to invest in the refurbishment of the bottom ash handling system at Unit 7 (315 MWe) and signed a contract with GE Power Romania for the turnkey supply of the above system. The existing Submerged Chain Conveyor (SCC) frequently failed, causing costly boiler shutdowns. Because of this issue, the EPC contractor turned to Magaldi to replace the wet system with the Magaldi Ash Post-combustor (MAP®).
The Solution
As a result of the wet-to-dry conversion, the Power Station registered an increase in boiler efficiency (2+%), a significant reduction in fuel consumption by the post-combustion of unburned fuel in the BA, and the elimination of methane as an auxiliary fuel for a stable combustion process.