The MRS® system
(Magaldi Mill Reject System)
A new process concept designed to mechanically handle rejects from coal mills, in a dry way
Rejects discharged from coal mills are a mixture of different materials (iron pyrites, rocks, tramp metal, etc.) with pulverized coal.
Magaldi engineered the MRS® system to ensure their dry removal and mechanical transport from coal pulverizing mills to bunkers, safely and reliably.
Temporarily stored in pyrite boxes, coal mill rejects are extracted by MRS® extractors and dosed onto the main MRS® conveyor, collecting the rejects produced by all coal mills. The MRS® system is designed to easily accommodate any increase in rejects and coal rate.
MRS® vs. conventional systems
Unlike conventional systems (hydraulic, pneumatic, or closed mechanical conveying systems), responsible for fire/explosion risks, low dependability due to chain damages or plugging, and premature wear, the MRS® system delivers a reliable, continuous operation, avoiding production losses and heavy maintenance and replacement costs.
Fire & explosion hazards reduction
Fire & explosion hazards - mainly occurring in presence of uncontrolled dust settlement, metal-on-metal contact, and sparks generated by pyrites - are a serious concern when handling coal mill rejects. That is why power plants using conventional conveyor systems are at risk for thousands to millions of dollars in damage and lost production.
Many drag chain conveyors feature chains running on the bottom pan and paddles that scrape along the floor and sidewalls. This friction creates an opportunity for sparks to form, thus increasing the likelihood of fire/explosions.
Likewise, usually deployed to reduce fugitive dust emissions and prevent outside contamination, conventional enclosed conveyors pose the potential for dust explosion hazards inside the enclosure. The latter creates a confined space where dispersed dust can reach an explosible concentration.
The MRS® system is less of a fire and explosion hazard. It is realized in “semi-open execution” that allows:
- Visual inspection while protecting operators from accidental contact with moving parts. On the contrary, with a closed machine, the inspection cannot be performed during operation due to the potentially explosive atmosphere;
- Fire and explosion risk reduction. The MRS® system allows for continuous dust settlement monitoring and optionally includes a dedusting system. Additionally, the conveyor is designed to avoid sliding friction among the moving parts, thus eliminating friction sparks and ensuring minimal metal-on-metal contact.
- Simpler design. Due to the inner explosive atmosphere, closed machines must be designed for an overpressure of 3.5 bar or higher. This prescription is not necessary with the MRS® system.
High reliability
The MRS® system also offers all the compelling benefits that derive from the use of the Superbelt® (steel belt) applied to mill rejects handling.
The Superbelt® is a steel belt conveyor made of a double-wire mesh with partially overlapped steel pans bolted on and supported by carrying idlers over its entire width. The driving force is transmitted by friction between the head pulley and the mesh belt, while a pneumatic take-up device on the tail pulley provides constant tension. Its unique design allows the trouble-free conveying of extremely hot, dusty, sharp, and abrasive materials, no matter if containing fines or lumps.
Unlike drag chain conveyors, the Superbelt® stands out for its high dependability. The multi-link design of the mesh belt ensures continuous operation, avoiding unexpected failures. One or more damage instances to the steel mesh do not lead to belt failure, allowing the system to keep running and postpone maintenance until a planned outage. In contrast, with a drag chain conveyor, the system’s reliability crucially depends on the chain links. As chain length increases, reliability decreases, causing more breakdowns and downtime.
Negligible wear
Concerning pneumatic and hydraulic sluice systems, which have high maintenance charges due to erosive wear or corrosion, wear on the Superbelt® is negligible as the material is conveyed slowly, with no relative motion against its steel parts.
Additionally, the Superbelt® also minimizes material build-ups and plugging risks.
Some successful stories
Mexico
Mill Reject Mechanical Handling
Coal-fired power plant
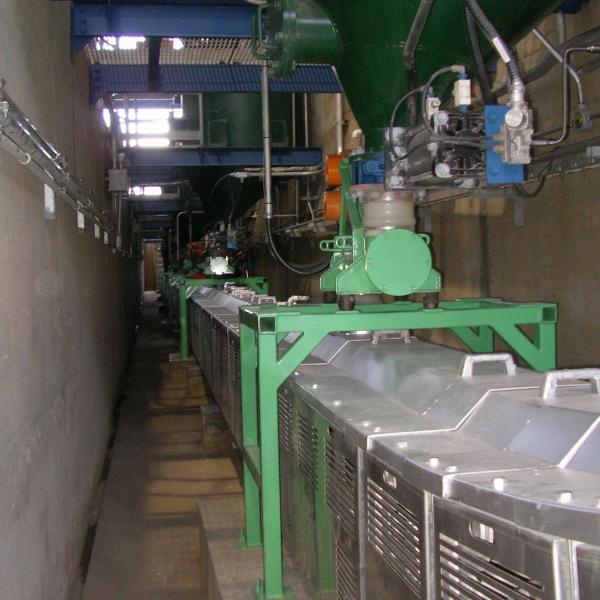
The performance evaluations carried out one year later the installation of the Magaldi equipment highlighted an overall availability of 99.8%: the best result ever achieved.
The Customer
The biggest electricity supplier in Latin America and the second most powerful state-owned company in Mexico.
The Challenge
Magaldi was requested to supply a complete solution for the dry removal of bottom ash, economizer ash, pre-heater ash, and milling rejects
The Solution
Along with the MRS® system, Magaldi also supplied a fully automated integrated supervision system and rubber belts for ash delivery to the final storage silo.
12 months after the hot commissioning of Unit #7 (700 MW), the Customer carried out an accurate performance analysis. The results of the investigation were astounding as the plant offered an overall availability of 99.8%: the best result ever achieved.
Magaldi was proud to be part of this result!
Italy
Mill Reject Mechanical Handling
Coal-fired power plant
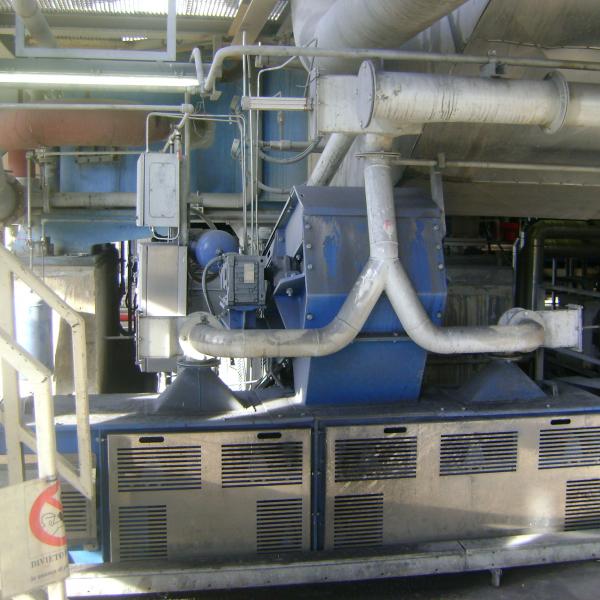
The supplied MRS® systems are fully compliant with the applicable ATEX European standards.
The Customer
Coal-fired power plant (3x660 MW ultra-supercritical boilers)
The Challenge
In 2008 Magaldi was requested to supply, install, and commission three Mill Reject Systems (MRS®) for the new PC boilers.
The Solution
Each unit features six coal mills (bowl type). From there, the rejects are discharged into pyrite boxes for temporary storage. Each box is provided with two knife gate valves, at inlet and outlet flanges, to disconnect the mill (at positive pressure) from the downstream equipment (at atmospheric pressure).
The rejects are intermittently extracted by short MRS® conveyors and dosed to the main MRS® conveyor, which collects the rejects from all coal mills. Finally, a bucket elevator discharges the material into the storage silo.
The MRS® systems meet the provisions of Directive 94/9/EC, commonly referred to as ATEX ("Atmosphères Explosibles") products directive, and the requirements of the Italian Fire and Rescue Authority.
Each MRS® system is integrated with:
- a de-dusting system to collect pulverized coal fines, thus lowering the fire and explosion hazards and avoiding dust dispersion to the environment;
- fire detection and protection system.