Le système MAC®
(Magaldi Ash Cooler)
Un système breveté d’extraction à sec, de refroidissement par air et de convoyage mécanique des mâchefers issus des chaudières à charbon pulvérisé.
Les inquiétudes relatives aux pénuries d’eau ainsi que les réglementations environnementales toujours plus rigoureuses incitent les centrales à charbon à se tourner vers les technologies de convoyage de cendres sèches.
Avec ses plus de 200 systèmes de convoyage de mâchefers secs installés dans le monde entier depuis 1985, tant pour des nouvelles chaudières que pour des rénovations d’installations, Magaldi est particulièrement bien placé pour démontrer les avantages de son système MAC® par rapport aux systèmes de convoyage de mâchefers humides.
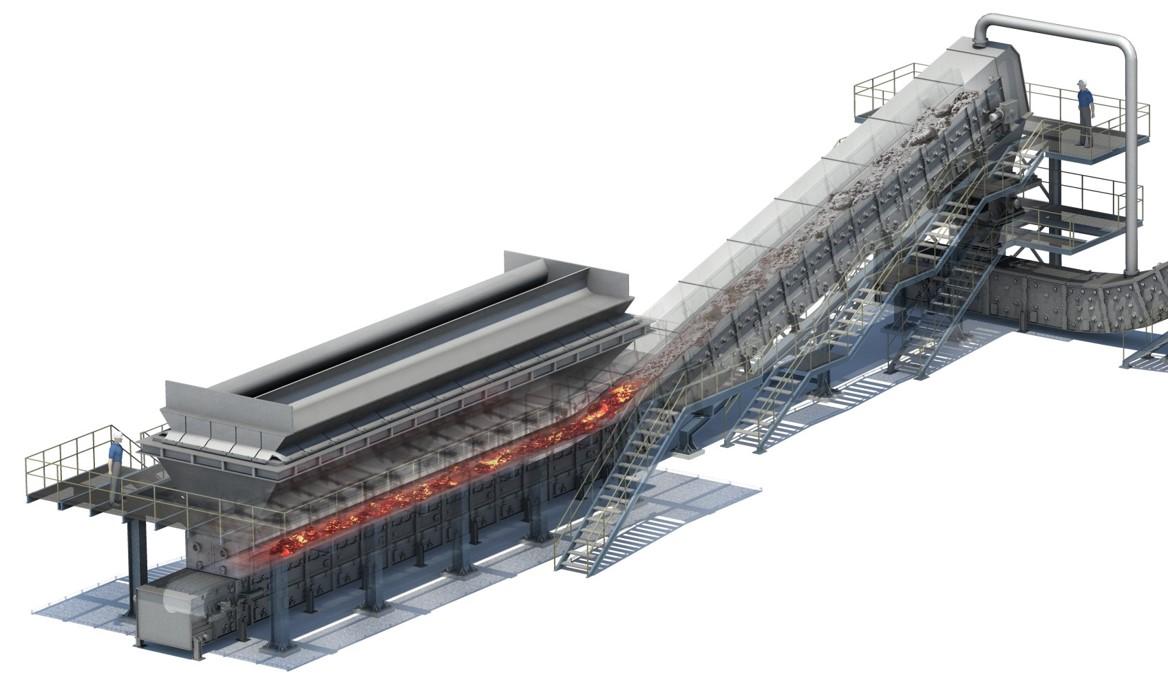
Mâchefers secs par rapport aux mâchefers humides
Contrairement aux systèmes de convoyage de mâchefers humides traditionnels - qui consomment énormément d’eau, coûtent cher en maintenance, posent des problèmes écologiques et ont des effets négatifs sur le fonctionnement des chaudières - le système MAC® (convoyage de mâchefers secs) garantit un fonctionnement fiable, rentable et respectueux de l’environnement en alliant à un processus de refroidissement à sec la fiabilité de la technologie de convoyage Superbelt®.
Économies d’eau et d’argent
Utiliser le système de convoyage de mâchefers secs (MAC®) permet d’économiser une très grande quantité d’eau.
Étant donné que le refroidissement et le convoyage des mâchefers se font sans eau, tous les équipements/systèmes auxiliaires (pompes, tuyauterie, bacs de déshydratation, installations de traitement des eaux, etc.) obligatoires dans les systèmes humides ne sont plus nécessaires. Tous les coûts d’exploitation et de maintenance associés disparaissent eux aussi.
Minime, la consommation d’eau ne sert qu’à la maîtrise des poussières au point de déchargement final. Lorsque l’eau est utilisée à des fins de dispersion des poussières, son débit fait l’objet d’un contrôle rigoureux.
Réduction des coûts d’élimination, augmentation de la valeur marchande des mâchefers
La mise en œuvre du système MAC® réduit également les coûts associés à l’élimination des cendres. La faible quantité d’eau utilisée fait aussi diminuer les frais de mise en décharge étant donné que les cendres pèsent beaucoup moins lourd.
Et plutôt que d’éliminer les mâchefers, il est possible de les transformer en sous-produits rentables en les broyant et en les vendant à des cimenteries vu que leurs caractéristiques (ils sont secs et à faible teneur en imbrûlés) augmentent leur valeur marchande.
Augmentation du rendement des chaudières et
atténuation des risques environnementaux
En fonction des propriétés réelles du charbon et des taux de cendres, installer un système MAC® permet d’augmenter les performances des chaudières de l’ordre de 0,1÷0,6 % (calcul dans le cadre de la norme ASME PTC4).
Une grande partie de la chaleur quittant le générateur de vapeur via l’ouverture inférieure (flux radiant du four, chaleur sensible et énergie chimique contenue dans les mâchefers en raison de leur teneur en carbone imbrûlé) est récupérée par l’air de refroidissement devenu chaud.
L’augmentation du rendement des chaudières entraîne parallèlement une diminution de la consommation de charbon, ce qui réduit les émissions de CO2 et permet donc une bonne atténuation des risques environnementaux.
Refroidissement supplémentaire et
convoyage vers le point de livraison final
La configuration standard du système MAC® comprend, en aval de la phase de concassage, le post-refroidisseur Magaldi (Ecobelt®). Ce deuxième convoyeur refroidit encore les mâchefers durant leur transport vers le point de livraison final.
Entièrement fermé dans une enveloppe en acier maintenue à pression légèrement négative, le convoyeur Ecobelt® est doté d’un système autonettoyant constitué de plaques en acier dûment profilées et articulées sur la bande. Sur la partie de retour de la bande, les plaques déplacent les fines vers l’arrière jusqu’à la section de queue où la chaîne Magaldi O-chain les recharge sur la bande principale.
Technologie de convoyage Superbelt®
En plus de garantir les avantages qui distinguent les systèmes secs des systèmes humides, le système MAC® doté de Superbelt® offre tous les atouts de ce convoyeur en matière de transport de cendres sèches, notamment:
- haute fiabilité
- résistance aux hautes températures
- haute résistance aux chocs
- usure négligeable et aucun problème de déchirures
- faible consommation énergétique
- maintenance simple et minimale
- sections de mesure de débit (en option).
Quelques projets réalisés
Colombia
Gestion des cendres de fond sec dans une centrale thermique à charbon
Centrale thermique à charbon
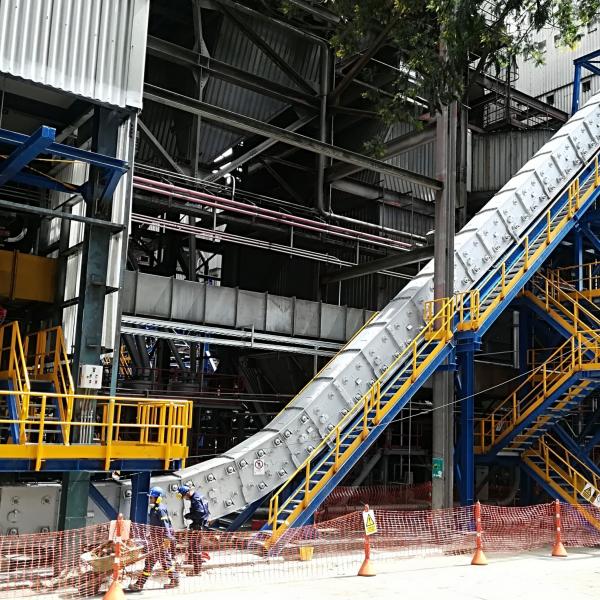
Le système Magaldi Dry Bottom Ash Handling est une solution fiable et écologique pour faire face au phénomène "El Niño".
Le Client
La centrale électrique a une capacité de génération installée totale de 236 MWe : l'unité #2 est conçue pour une production électrique brute à charge nominale de 38 MWe, tandis que les unités #3, #4 et #5 ont chacune une production électrique brute de 66 MWe. Toutes les unités de génération sont basées sur des chaudières à charbon pulvérisé (PC).
Le Défi
Ces dernières années, la Colombie a affronté sa plus grande crise énergétique en raison des effets catastrophiques du phénomène "El Niño", qui a entraîné une sécheresse extrême et compromis la stabilité de l'approvisionnement énergétique du pays. Pour faire face à cette urgence, le Client a décidé de remplacer le système humide existant par un système sec plus fiable.
La Solution
Quatre systèmes MAC® ont été installés sous les unités #2, #3, #4 et #5 pour augmenter la fiabilité de la centrale et générer de l'énergie propre.
Le premier système MAC® est pleinement opérationnel depuis juillet 2018, le second a été installé en septembre, tandis que les démarrages des deux autres systèmes ont respectivement eu lieu en novembre 2018 et janvier 2019. Magaldi a fourni une solution clé en main pour l'évacuation des cendres de fond, depuis les points de terminal des chaudières jusqu'à leur déchargement dans des camions ouverts, y compris les équipements électriques, les structures de support en acier et le silo de stockage des cendres.
États-Unis
Gestion des cendres de fond sec dans une centrale thermique à charbon
Centrale thermique à charbon
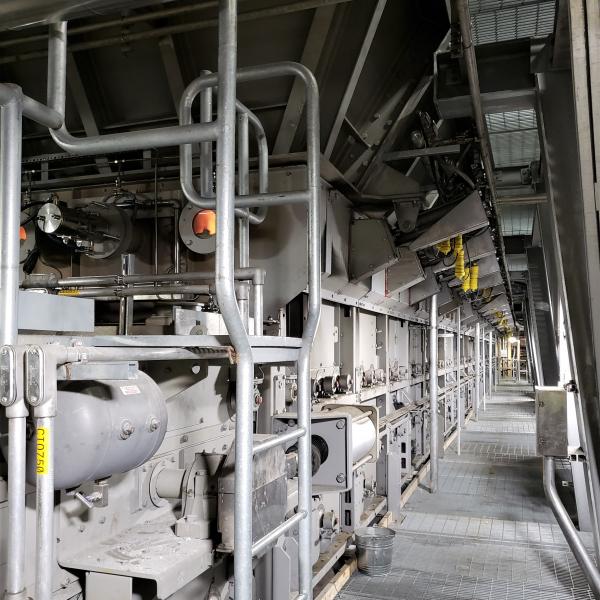
La technologie sèche de Magaldi a été installée sur les quatre unités pour répondre aux normes de l'EPA. Elle a amélioré la centrale du point de vue de la sécurité, des opérations, de la maintenance et de l'entretien.
Le Client
Avec une capacité de génération installée de près de 3 600 MWe, la centrale électrique est l'une des plus grandes installations de production d'électricité aux États-Unis, la plus grande centrale alimentée exclusivement au charbon.
La Défi
Le Client devait se conformer aux réglementations environnementales (CCR/ELG) imposant de nouvelles normes pour limiter l'utilisation des eaux et des bassins à cendres.
La Solution
Le système MAC® a permis de résoudre tous les problèmes liés à l'eau – tant opérationnels qu'environnementaux – associés aux bacs de déshydratation, au traitement des eaux usées, aux pompes, aux échangeurs de chaleur, à la corrosion du contrôle du pH, aux fuites d'eau, aux éclaboussures d'eau chaude ou explosions de vapeur, au risque de glace dans les climats froids, à la pollution des bassins, etc.
De plus, il s'est révélé être moins exigeant en maintenance que toute autre technologie sur le marché.
Japon
Gestion des cendres de fond sec dans une centrale thermique à charbon
Centrale thermique à charbon
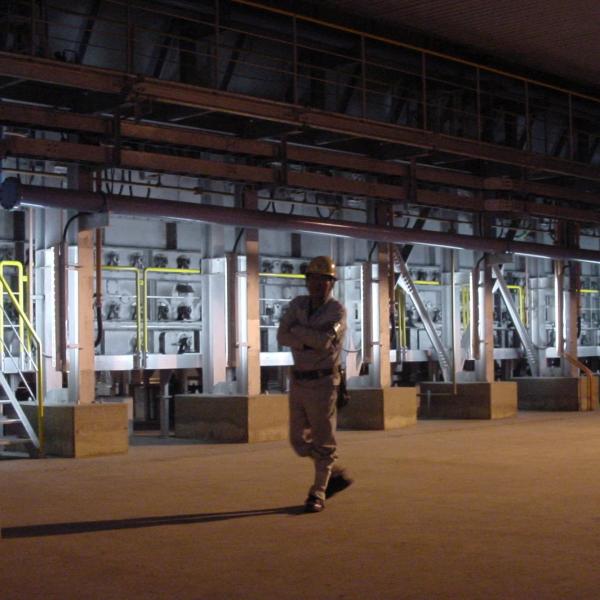
test
Le Client
L'une des centrales thermiques à charbon les plus efficaces au monde. Magaldi a reçu la commande d'installer son système de gestion des cendres sèches sur l'Unité n°3 (600 MWe).
Le Défi
Après la catastrophe nucléaire de Fukushima Daiichi, toutes les centrales nucléaires japonaises ont été fermées pour des raisons de sécurité. Cette décision a entraîné une augmentation de la consommation de combustibles fossiles et, par conséquent, une vague de nouvelles constructions de centrales à charbon vertes.
Avec son licencié japonais Kawasaki Heavy Industries (KHI), Magaldi a participé à ce "printemps du charbon".
LaSolution
Magaldi était responsable du système depuis la conception et la fabrication jusqu'à l'approvisionnement des équipements et l'installation.
Le système de gestion des cendres est installé sur l'Unité 3, qui est ajoutée à la centrale thermique pour produire 600 MW de puissance. Le système est composé d'un sous-système pour la gestion des cendres volantes (cendres volantes dans les gaz d'échappement) capturées par un précipitateur électrostatique et d'un sous-système pour la gestion des cendres de fond (également appelées cendres de clinker) provenant du bas du four. Les cendres de fond sont traitées à sec. L'ancienne méthode de gestion humide utilisait de l'eau pour refroidir et transporter les cendres de fond, qui étaient ensuite déshydratées et transportées vers le site d'élimination des cendres par camion ou autre méthode. En revanche, la méthode sèche utilise de l'air pour refroidir les cendres de fond tout en les transportant à sec. Cela réduit l'impact environnemental, diminue les coûts et économise de l'espace en éliminant le besoin d'équipements tels que pour l'approvisionnement en eau, le traitement des eaux usées, la déshydratation et le stockage de l'eau. Cela augmente également l'efficacité de la chaudière et permet des économies d'énergie, par exemple en permettant la récupération de la chaleur sensible des cendres de fond, de la chaleur de réaction du carbone non brûlé et de la chaleur radiante du four.