Système MRS®
(Magaldi Mill Reject System)
Un nouveau concept de procédé permettant un convoyage mécanique à sec des refus des broyeurs à charbon.
Les refus des broyeurs à charbon consistent en différents matériaux (pyrites de fer, roches, débris métalliques, etc.) mélangés à du charbon pulvérisé.
Magaldi a conçu le système MRS® afin d’assurer leur évacuation à sec et leur transport mécanique depuis les broyeurs à charbon jusqu’aux soutes de manière fiable et sûre.
Stockés temporairement dans des caisses à pyrites, les refus des broyeurs à charbon sont extraits par les extracteurs MRS® puis dosés sur le convoyeur MRS® principal qui collecte les refus produits par tous les broyeurs à charbon. Le système MRS® a été conçu pour s’adapter facilement à toutes les hausses de refus et de taux de charbon.
Système MRS® par rapport aux systèmes traditionnels
Contrairement aux systèmes traditionnels (systèmes de convoyage hydrauliques, pneumatiques ou mécaniques fermés) qui peuvent présenter des risques d’incendie/d’explosion, poser des problèmes de fiabilité causés par des colmatages ou des endommagements de chaînes ou s’user prématurément, le système MRS® se distingue par un fonctionnement fiable et continu qui permet d’éviter les pertes de production ou des coûts élevés de maintenance ou de remplacement.
Réduction des risques d’incendie ou d’explosion
Favorisés principalement par la présence de dépôts de poussière incontrôlés, de contacts métal sur métal ou d’étincelles générées par les pyrites, les risques d’incendie ou d’explosion constituent un problème majeur dans le convoyage des refus des broyeurs à charbon. C’est pourquoi les centrales utilisant des systèmes de convoyage traditionnels risquent des milliers voire des millions de dollars en termes de dommages et de perte de production.
De nombreux convoyeurs à chaîne traînante sont équipés de chaînes fonctionnant sur un plateau inférieur et de palettes qui raclent le sol et les parois latérales. Cette friction peut provoquer des étincelles et ainsi augmenter les risques d’incendie/d’explosion.
De même, les convoyeurs fermés traditionnels généralement utilisés pour réduire les échappées de poussières et éviter les contaminations extérieures présentent des risques potentiels d’explosion des poussières à l’intérieur de l’enveloppe. Cette dernière crée en effet un espace confiné au sein duquel les poussières dispersées peuvent atteindre une concentration explosible.
Le système MRS® présente moins de risques d’incendie et d’explosion. Il est en effet réalisé en « exécution semi-ouverte » qui permet :
- L’inspection visuelle tout en protégeant les opérateurs de tout contact accidentel avec les pièces en mouvement. Les équipements fermés en revanche ne permettent pas d’effectuer des inspections durant le fonctionnement en raison de l’atmosphère potentiellement explosive ;
- Réduction des risques d’incendie et d’explosion Le système MRS® permet de surveiller en continu le dépôt de poussières et peut comprendre en option un système de dépoussiérage. De plus, le convoyeur a été conçu pour éviter les frictions de glissement entre les pièces mobiles et ainsi éliminer les étincelles de frottement tout en minimisant les contacts métal sur métal.
- Une conception plus simple. En raison de l’atmosphère explosive interne, les machines fermées doivent être conçues en vue d’une surpression de 3,5 bar ou plus. Cette prescription n’est pas nécessaire pour le système MRS®.
Haute fiabilité
Le système MRS® offre également tous les avantages majeurs associés à l’utilisation de Superbelt® (bande métallique) pour le convoyage des refus de broyeurs.
Le Superbelt® est un convoyeur à bande métallique constitué d’écailles en acier partiellement superposées et boulonnées sur un système à maille à double fil soutenu par des rouleaux porteurs sur toute sa largeur. La force motrice est transmise par friction entre le tambour de tête et la bande maillée tandis qu’un dispositif de mise en tension pneumatique sur le tambour de queue assure une tension constante. Sa conception particulière permet de convoyer sans problèmes des matériaux extrêmement chauds, poussiéreux, tranchants ou abrasifs, ceci aussi bien sous forme de blocs que de particules fines.
Contrairement aux convoyeurs à chaîne traînante, le Superbelt® se distingue par sa grande fiabilité. La conception multi-liens de la bande maillée garantit un fonctionnement continu et évite les défaillances imprévues. Si la maille métallique est endommagée à un ou plusieurs endroits, cela n’entraîne pas la panne de toute la bande et le système continue à fonctionner, ce qui permet de reporter la maintenance à l’interruption de fonctionnement programmée. Au contraire, avec les convoyeurs à chaîne traînante, la fiabilité du système dépend complètement des maillons de la chaîne. Plus la longueur de la chaîne augmente, plus la fiabilité diminue, ce qui entraîne davantage de pannes et de temps d’arrêt.
Usure négligeable
Par rapport aux systèmes de transport hydraulique ou pneumatique, particulièrement coûteux en termes de maintenance en raison de la corrosion et de l’usure par érosion, le Superbelt® se distingue par une usure négligeable car les matériaux sont convoyés lentement et sans mouvement relatif contre les pièces en acier.
De plus, le Superbelt® minimise également les accumulations de matériaux et les risques de colmatage.
Quelques projets réalisés
Mexique
Transport à sec des pyrites des broyeurs à charbon
Centrale thermique à charbon
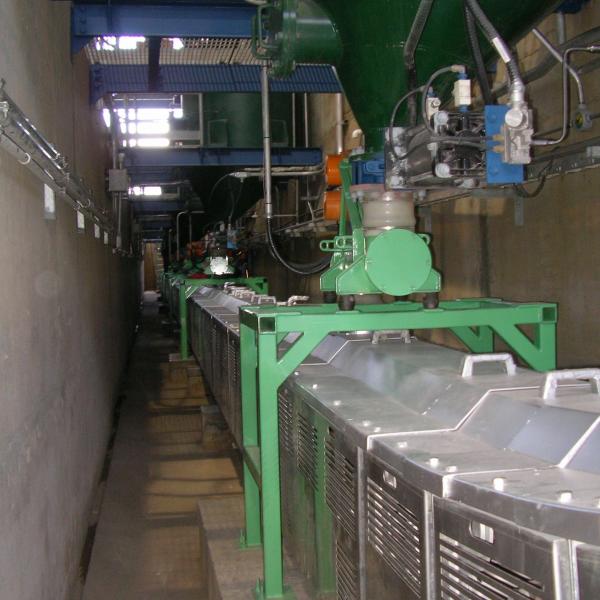
La surveillance des performances réalisée un an après l'installation des systèmes Magaldi a révélé une disponibilité totale de 99,8 % : le meilleur résultat jamais atteint.
Le Client
Le plus grand fournisseur d’électricité en Amérique latine et la deuxième entreprise publique la plus puissante du Mexique.
Le Défi
Magaldi a été sollicitée pour fournir une solution complète pour le transport à sec des cendres lourdes, des cendres des économiseurs, des cendres de préchauffeur et des pyrites.
La Solution
En plus du système MRS®, Magaldi a également fourni un système de supervision intégré entièrement automatisé et des bandes transporteuses en caoutchouc pour le transport des cendres vers le silo de stockage final.
Un an après la mise en service de l’unité #7 (700 MW), le client a effectué une analyse détaillée des performances. Les résultats de l’étude ont été stupéfiants, car l’usine a atteint une disponibilité totale de 99,8 % : le meilleur résultat jamais obtenu.
Magaldi est fière d’avoir contribué à ce résultat extraordinaire !
Italie
Transport à sec des pyrites des broyeurs à charbon
Centrale thermique à charbon
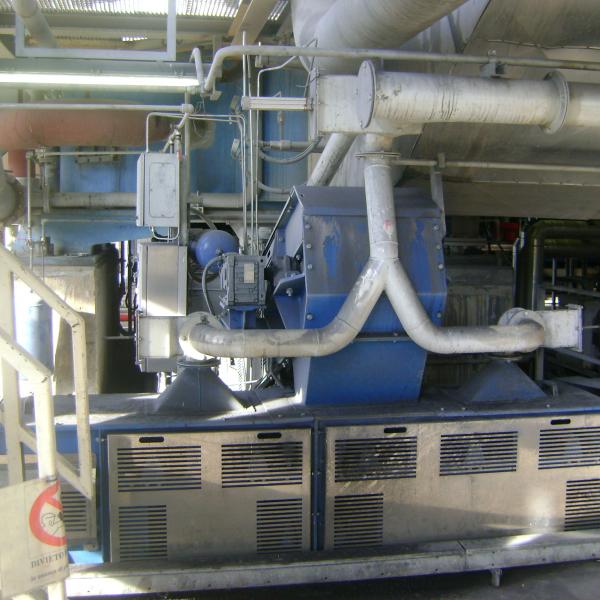
Les systèmes MRS® sont conformes aux normes européennes ATEX.
Le Client
Centrale à charbon (3x660 MW chaudières ultra-supercritiques).
Le Défi
En 2008 Magaldi a été sollicitée pour fournir, installer et mettre en service trois systèmes MRS® pour les nouvelles chaudières.
La Solution
Chaque unité dispose de six broyeurs à charbon. Les déchets sont ensuite déversés dans des bacs (pyrite box) pour un stockage temporaire.
Les déchets sont extraits de manière intermittente par de petits convoyeurs MRS® et dosés dans le convoyeur MRS® principal, qui collecte les déchets de tous les broyeurs. Enfin, un élévateur à godets déverse le matériau dans le silo de stockage.
Les systèmes MRS® respectent les dispositions de la directive 94/9/CE, communément appelée la directive ATEX (Atmosphères Explosibles), ainsi que les exigences de l'Autorité italienne de secours et de lutte contre l'incendie.
Chaque MRS® est équipé de:
- un système de dépoussiérage pour collecter les poussières fines de charbon, réduisant ainsi les risques d'incendie et d'explosion et évitant la dispersion des poussières dans l'environnement ;
- un système de détection d'incendie.