Convoyeur Superbelt®
Un moyen efficace de convoyer les recettes de chargement depuis l’accumulateur de rebuts jusqu’à la trémie d’alimentation de la plateforme de fusion.
Il est certes possible d’utiliser des convoyeurs et des systèmes de convoyage traditionnels pour charger les fours ou transporter des charges lourdes mais ils ne sont pas conçus pour résister à la chaleur et à des impacts réitérés dans le temps.
Le convoyeur Superbelt® se distingue de toutes les technologies concurrentes. Conçu pour résister aux conditions de fonctionnement les plus difficiles, il peut non seulement transporter des matériaux lourds sans les ne déverser ni les endommager mais aussi supporter les contraintes thermiques des environnements de travail des fours à haute température.
Haute fiabilité
Le convoyeur Superbelt® est constitué d’écailles en acier partiellement superposées et solidement boulonnées sur un système breveté à maille à double fil.
La conception multi-lien de la bande garantit une redondance, un entretien minimal ou inexistant et un fonctionnement continu sans interruptions. Même si la maille est gravement endommagée, le convoyeur continuera à fonctionner jusqu’à l’arrêt prévu pour la maintenance programmée sans pannes soudaines.
Permettant de préserver la productivité et la rentabilité de toute l’installation, le fonctionnement sans imprévus se traduit par des gains d’efficacité et de disponibilité, ceci 24 heures sur 24, 7 jours sur 7, toute l’année.
Résistance aux chocs
Dotée d’un cadre amortisseur de choc, d’une résistance exceptionnelle, la structure portante de la bande est conçue pour supporter de gros impacts. Le convoyeur repose sur toute sa largeur sur des rouleaux porteurs spécialement conçus pour résister aux chocs. Au niveau des points de chargement, ces rouleaux porteurs peuvent être rapprochés.
La section de chargement et la bande elle-même peuvent être fabriquées en acier au manganèse afin de garantir la plus haute résistance possible à la corrosion et à la déformation. Les écailles sont généralement réalisées en acier au manganèse d’une dureté de 400 HB et d’une épaisseur de 8+8 mm.
Résistance à la chaleur et à l’usure
En raison des températures élevées de l’environnement de travail, les opérations de fusion peuvent mettre à rude épreuve les systèmes de convoyage. L’exposition à la chaleur provoque des dilatations thermiques qu’il est nécessaire de pallier ainsi qu’une usure rapide.
Grâce à une méthode brevetée d’assemblage des écailles à la bande maillée permettant à tous les composants de se dilater librement dans n’importe quelle direction sans provoquer de déformations permanentes, le convoyeur Superbelt® résout tous les problèmes liés à la chaleur. Il en résulte un convoyeur à même de résister à des températures allant jusqu’à 1100 °C sans affecter la résistance à l’abrasion de l’équipement.
Niveaux de sécurité élevés
Dans la mesure où il élimine les interventions manuelles dans le convoyage des rebuts, le convoyeur Superbelt® améliore radicalement la sécurité au travail. Moins de chariots élévateurs circulent, la production devient plus ergonomique et les opérateurs peuvent rester à une distance de sécurité des hautes températures des fours de fusion.
Par ailleurs, le risque de débordement de matériaux est pratiquement nul grâce aux bavettes hautes suivant le profil des parois latérales de la bande sur toute sa longueur, ce qui permet de contenir même les matériaux les plus susceptibles de se déverser.
Préchauffage de la charge (facultatif)
Le préchauffage de la recette de chargement a une incidence positive sur le bilan énergétique et la productivité du four de fusion. En option, la technologie Superbelt® permet de l’effectuer sur le système de convoyage.
Avant d’atteindre le four de fusion, la recette de chargement pénètre dans la chambre de préchauffage afin d’être séchée (si nécessaire) puis chauffée par une batterie de brûleurs à gaz. La chambre est divisée en plusieurs zones permettant un réglage indépendant des rendements thermiques des brûleurs en vue d’une meilleure maîtrise de la température du matériau et d’une plus grande flexibilité concernant le séquençage durant l’indexation de la charge de matériau de chaque lot.
Mesure de débit de matériau (en option)
Le convoyeur Superbelt® peut également être doté d’une mesure de débit de matériau. La section de la bande est alors équipée d’un châssis spécial doté de cellules de charge et d’une unité de commande électronique en vue des calculs de masse et de débit en temps réel.
Le débit de matériau réel est calculé à partir de la vitesse de la bande, obtenue via un encodeur, et du signal de débit émis par les cellules de charge.
Quelques projets réalisés
Italia
Carico forno
Fonderia di ghisa
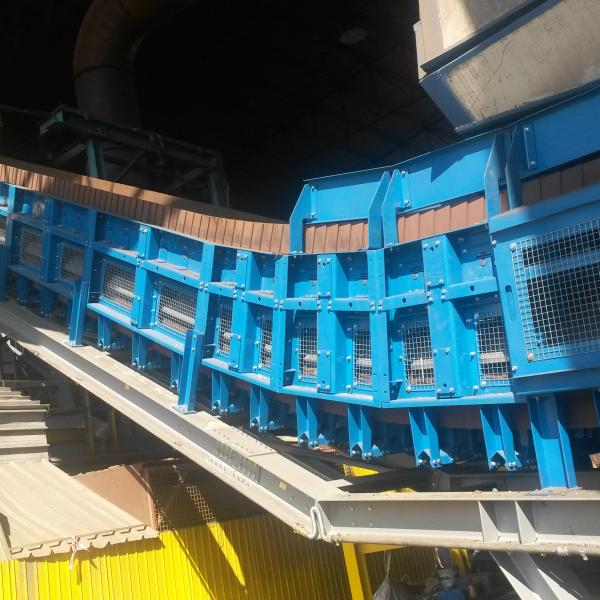
Il trasportatore Superbelt® ha ridotto drasticamente i costi di manutenzione e i tempi di fermo macchina.
Il Cliente
Fonderia specializzata nella produzione di getti in ghisa sferoidale per applicazioni sanitarie e domestiche.
La Sfida
Il trasportatore a catena utilizzato per caricare i forni (EAF) era soggetto a continue rotture. La fonderia aveva bisogno di una soluzione decisamente più affidabile.
Dieci anni prima, la Magaldi aveva installato un trasportatore a nastro Superbelt® a valle della granigliatrice, per la smaterozzatura (tramite cunei idraulici) e la cernita delle fusioni. Dopo averne sperimentato i vantaggi, non c'erano dubbi sulla scelta del nuovo trasportatore per carico forno.
La Soluzione
Un Superbelt® inclinato di 30° trasporta le materozze dalla tramoggia di pesatura fino ai 2 forni, offrendo massima affidabilità.
Il cliente ha riferito che i costi di manutenzione e i tempi di fermo sono stati drasticamente ridotti.
Messico
Carico forno
Fonderia di rame
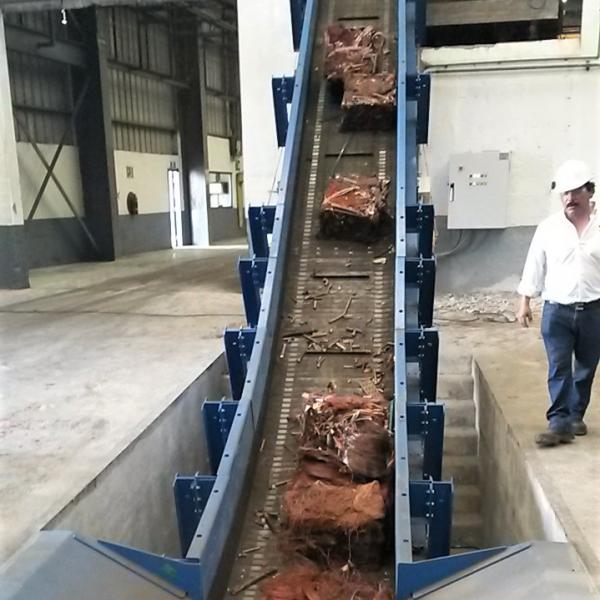
Il trasportatore Superbelt® ha ridotto drasticamente i rischi alla sicurezza degli operatori, eliminando il contatto con i rottami e diminuendo il traffico dei carrelli elevatori all'interno dello stabilimento.
Il Cliente
Impianto di fusione secondaria del rame.
La Sfida
Sostituire il sistema di carico forno esistente, fonte di rischi per la sicurezza degli operatori.
Stoccati in un bunker, i rottami venivano pressati in balle e scaricati nel vibro-alimentatore mediante un carrello elevatore. Il vibro-alimentatore si muoveva su binari per avvicinarsi al forno e scaricarvi i rottami.
Il carrello elevatore funzionava in modo pericoloso poichè la piattaforma vibrante era troppo alta per essere raggiunta agevolmente dal carrello. Inoltre, la movimentazione del materiale all’interno dello stabilimento risultava difficile e costosa.
La Soluzione
Il trasportatore Superbelt® è dotato di una tramoggia di carico progettata ad hoc ed installata in una fossa per consentire agli operatori di caricare più facilmente i rottami e gestire il processo in batch.
Sebbene il trasportatore abbia una inclinazione di 35°, le balle di rame vengono movimentate senza problemi grazie al nastro provvisto di setti che impediscono al materiale di rotolare all'indietro.
India
Carico forno
Fonderia di ghisa
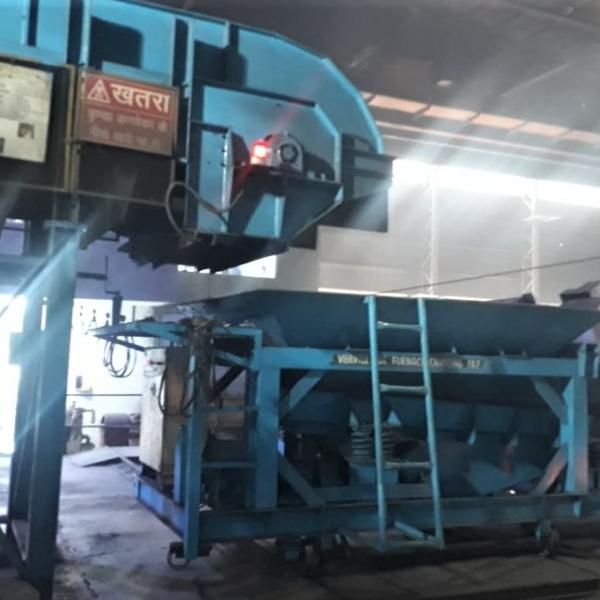
Automatizzando il trasporto dei rottami, il Superbelt® ha ridotto i tempi di ciclo e aumentato la sicurezza degli operatori, non più esposti a fonti di calore nè ai rischi legati alla movimentazione di materiali pesanti e taglienti.
Il Cliente
Produttore di getti in ghisa per il settore automotive
La sfida
Assicurare elevati livelli di sicurezza nel trasporto rottami per carico forno.
La Soluzione
Inizialmente intenzionato a caricare il forno con gru EOT, il Cliente ha successivamente optato per 2 trasportatori Superbelt® che offrono un migliore controllo del processo di carico forno.
Nella stessa fonderia la Magaldi aveva già sostituito un vibrante installato tra il tamburo di raffreddamento DISA e la granigliatrice, responsabile di frequenti danni ai getti. L'installazione del Superbelt® aveva risolto il problema e consentito di realizzare la smaterozzatura dei getti sullo stesso nastro. Un secondo Superbelt® era poi stato installato a valle della granigliatrice per la cernita delle fusioni.