Der Superbelt® Stahlbandförderer
Geeignet für die harten Bedingungen unter der Schere
Rohrhersteller müssen heute mehr denn je die Betriebszeit maximieren und das Schrottrecycling fördern. Im Einklang mit den Grundsätzen der Kreislaufwirtschaft wird der gesamte Schrott aus der nachgelagerten Rohrproduktion gesammelt und im Stahlherstellungsprozess wiederverwendet, um die Produktionskosten zu senken und den ökologischen Fußabdruck des Unternehmens zu minimieren. Dieser Prozess stellt jedoch hohe Anforderungen an die Materialhandhabungsgeräte, da die Rohre und der Schrott in vielen verschiedenen Formen und Gewichten aus der Schere kommen.
Der Superbelt® Stahlbandförderer ist eine sehr robuste und schwere Konstruktion, die für eine Vielzahl von Schrottarten geeignet ist und die nötige Flexibilität bei der Schrottverarbeitung bietet.
Hohe Zuverlässigkeit
Der Superbelt® Stahlbandförderer verfügt über teilweise überlappende Stahlwannen, die auf einem patentierten doppelten Maschendrahtsystem aus Stahl fest verschraubt sind.
Das schadenstolerante Design des Bands basiert auf einem mehrgliedrigen Konzept: Der Maschendraht sorgt für Redundanz, wenig bis gar keine Wartung und einen störungsfreien Dauerbetrieb. Selbst wenn der Maschendraht stark beschädigt wird, läuft der Förderer ohne plötzliche Ausfälle bis zur geplanten Wartung weiter.
Hohe Schlagzähigkeit
Die Tragstruktur des Förderers ist mit einem stoßdämpfenden Rahmen ausgestattet, der den Aufprall von herabfallendem Material abfängt.
Speziell konstruierte Tragrollen sind entlang der Bandbreite angeordnet und können in der Lastzone eng beieinander liegen. Maschen- und Bandwannen können aus Manganstahl hergestellt werden, um die höchste Widerstandsfähigkeit gegen Korrosion und Verformung sicherzustellen.
Sicherer Betrieb und kein Verschütten von Material
Der Superbelt® Stahlbandförderer bietet ein hohes Maß an Sicherheit bei der Förderung von Scherschrott.
Hohe Schürzen folgen dem Seitenwandprofil des Bands über die gesamte Länge, um auch die größten Materialschwälle aufzufangen. Außerdem entsteht durch den Hochdruckkontakt im überlappenden Wannenbereich eine dichte Versiegelung, die jegliches Verschütten verhindert und das Risiko von Materialaufprall durch die scharfen Kanten vermeidet.
All das trägt dazu bei, ein sichereres Arbeitsumfeld zu schaffen.
Optionale Materialverwiegung
Der Superbelt® Stahlbandförderer kann auch mit einer optionalen Materialverwiegung ausgestattet werden. In diesem Fall ist der Wiegebandabschnitt mit einem speziellen Rahmen mit Wägezellen und einer elektronischen Steuereinheit für die Berechnung von Masse und Geschwindigkeit in Echtzeit ausgestattet.
Der tatsächliche Materialdurchsatz wird durch die Kombination der Bandgeschwindigkeit, die von einem Encoder überwacht wird, und dem Gewichtssignal der Wägezellen bestimmt.
Einige Erfolgsgeschichten
Mexiko
Förderung von heißem Schredderschrott
Integriertes nahtloses Rohrwerk
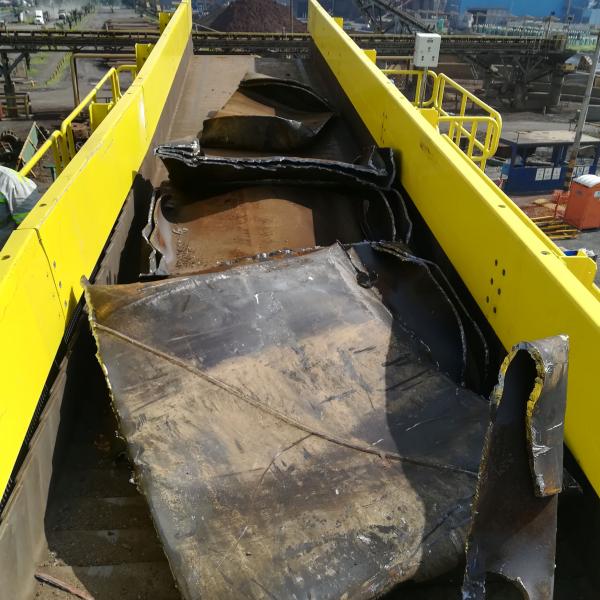
Dank ihrer hohen Flexibilität ermöglichten die Superbelt®-Förderer die optimale Verteilung des Stahlschrotts auf der gesamten verfügbaren Fläche.
Der Kunde
Stahl wird aus Schrott und Eisenschwamm hergestellt, der zu Knüppeln und nahtlosen Rohren verarbeitet wird. Der beim Schneiden von Rohren anfallende Stahlschrott wird zur Beschickung eines Elektrostahlwerks verwendet.
Die Herausforderung
Ursprünglich wurde der Schrott mit Lastwagen zum Schmelzwerk transportiert. Dieses Verfahren war sehr teuer und führte zu Ineffizienzen bei der Verwaltung des verfügbaren Platzes.
Die Lösung
Magaldi installierte zwei Superbelt®-Förderer, um gepressten Rohrschrott (90%) und anderen Metallschrott (10%) von der automatischen Schermaschine zum Schrottplatz zu befördern. Das erste Förderband ist feststehend und besteht aus Stahl-Verschleißwannen mit geformten Wülsten und Verstärkungsrippen. Der Ladebereich ist so konstruiert, dass er dem Aufprall der schweren Teile standhält, die vom schwenkbaren Zerkleinerungsband entladen werden. Außerdem sind beide Seiten des Förderkanals mit verschleißfesten Wannen ausgekleidet, um die Reibung und das Verklemmen des Materials zu minimieren.
Der zweite Superbelt®-Förderer ist so konstruiert, dass er über eine gebogene Stahlschiene schwenkt. Dank seines exklusiven Designs bietet der Förderer die Möglichkeit, das Material über eine größere Fläche des Schrottplatzes abzuladen und so den verfügbaren Platz optimal zu nutzen.
USA
Förderung von heißem Schredderschrott
Integriertes Mini-Walzwerk
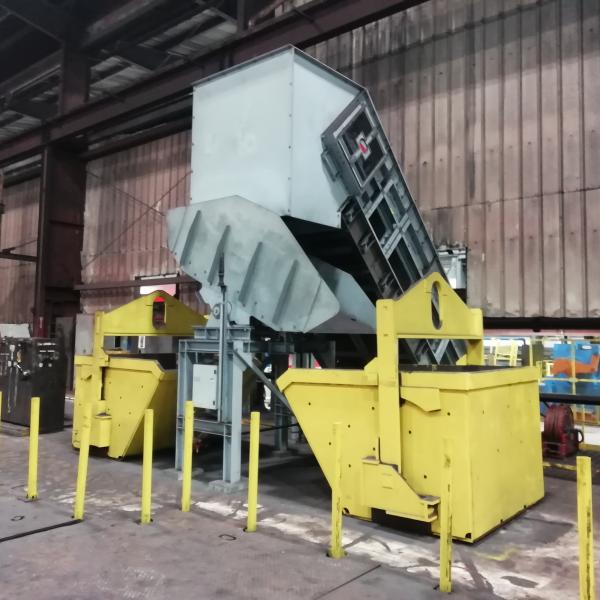
Geeignet für extremere Temperaturen und anspruchsvolle, harte Betriebsbedingungen.
Der Kunde
Voll integriertes Mini-Walzwerk mit einem hochmodernen Schmelzbetrieb und einer Walzanlage.
Die Herausforderung
Der Kunde musste das Schmelzwerk mit einem zuverlässigen Förderer ausstatten, der in der Lage ist, Scherschrott bei hohen Temperaturen zu transportieren.
Die Lösung
Ein Superbelt®-Förderer transportiert die geschnittenen Stäbe von der Schermaschine zum Betriebsbereich, wo das Material in zwei Schaufeln entladen wird. Eine Entladerutsche leitet die Stäbe in die Schaufeln, um den ersten zu entladen, während der zweite befüllt wird.
Das Superbelt® ist mit einer Neigung von 45° konstruiert und befördert zwei Arten von heißen (1093°C) Scherabfällen:
- Scherenschnitte unter normalen Betriebsbedingungen;
- Schrottscheiben unter erschwerten Bedingungen.
Ausgehend von den Auslegungsdaten beträgt die Ernteabschlagsrate 3,05 t/h, während die für die Beförderung von Schrottscheiben erforderliche Schwallleistung unter Störungsbedingungen 272,2 t/h beträgt. Im letzteren Fall passt das gesamte Walzwerksteuerungssystem die Bandgeschwindigkeit automatisch an, bis die Störung überwunden ist. Aus diesem Grund wurde ein Frequenzumrichter am Antrieb des Förderers installiert.
USA
Förderung von heißem Schredderschrott
Rohrwerk
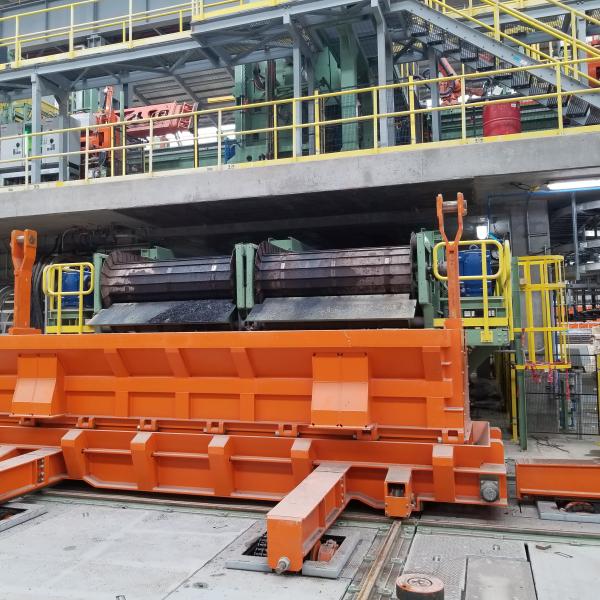
Geeignet für die harten Bedingungen unter Scheren in Schrottverarbeitungsanlagen.
Der Kunde
Führender Anbieter von Rohren, Futterrohren und Schläuchen.
Die Herausforderung
Der EPC-Auftragnehmer wandte sich an Magaldi, um eine zuverlässige Lösung für die automatische Förderung von Spänen und Schrott zu finden, die bei der Endbearbeitung anfallen.
The Solution
Magaldi lieferte 5 Superbelt®-Förderer, um Schrott und Späne von den Schermaschinen abzutransportieren.
Die vier in einer Grube installierten Förderer sind mit einer speziell entwickelten Verladerutsche ausgestattet. Die Wannen sind aus Hardox 400, um Abnutzung und schweren Stößen zu widerstehen, da das Material manchmal in Klumpen auftreten kann. In den Förderern ist ein zentrales Schmiersystem installiert, das eine konstante Schmierung der Tragrollen und Trommellager erlaubt.
Der fünfte Superbelt® bearbeitet das Material, das von einer Wasserschneidemaschine kommt. Wegen der Anwesenheit von Wasser sind die Wannen und das Maschenband aus rostfreiem Stahl gefertigt.